Hot work die steel material and preparation method thereof
A technology of hot work die steel and die, which is applied in the field of steel processing, can solve the problems affecting the use effect of hot work die steel, hardness reduction, etc., and achieve the effects of high utilization rate, reduced quenching cost, and low raw material loss
- Summary
- Abstract
- Description
- Claims
- Application Information
AI Technical Summary
Problems solved by technology
Method used
Image
Examples
Embodiment 1
[0025] A hot work die steel material, wherein the raw materials used (by weight percentage) include carbon 0.4wt%, chromium 1.1wt%, vanadium 0.2wt%, tungsten 0.3wt%, molybdenum 0.7wt%, copper 0.7wt%, Manganese 2.3wt%, nickel 0.7wt%, silicon 0.3wt%, iron 93.3wt%.
[0026] A method for preparing a hot work die steel material, the specific preparation steps are:
[0027] Step 1. Initial refining: put iron and carbon into an intermediate frequency induction furnace for smelting according to the ratio of raw materials to obtain base molten steel, and then transfer the base molten steel into a vacuum refining furnace for vacuum refining to prepare refined molten steel;
[0028] Step 2. Mixing: transfer the refined molten steel into the intermediate frequency induction furnace, then add chromium, vanadium, tungsten, molybdenum, copper, manganese, nickel, silicon to the intermediate frequency induction furnace in sequence according to the ratio of raw materials, melt and mix them , t...
Embodiment 2
[0040] A hot work die steel material, wherein the raw materials used (by weight percentage) include carbon 0.6wt%, chromium 2.3wt%, vanadium 0.8wt%, tungsten 0.5wt%, molybdenum 0.9wt%, copper 1.3wt%, Manganese 4.4wt%, nickel 0.9wt%, silicon 0.4wt%, iron 87.9wt%.
[0041] A method for preparing a hot work die steel material, the specific preparation steps are:
[0042]Step 1. Initial refining: put iron and carbon into an intermediate frequency induction furnace for smelting according to the ratio of raw materials to obtain base molten steel, and then transfer the base molten steel into a vacuum refining furnace for vacuum refining to prepare refined molten steel;
[0043] Step 2. Mixing: transfer the refined molten steel into the intermediate frequency induction furnace, then add chromium, vanadium, tungsten, molybdenum, copper, manganese, nickel, silicon to the intermediate frequency induction furnace in sequence according to the ratio of raw materials, melt and mix them , to...
Embodiment 3
[0055] A hot work die steel material, wherein the raw materials used (by weight percentage) include carbon 0.7wt%, chromium 3.5wt%, vanadium 1.5wt%, tungsten 0.8wt%, molybdenum 1.2wt%, copper 2.1wt%, Manganese 5.5wt%, nickel 1.1wt%, silicon 0.5wt%, iron 83.1wt%.
[0056] A method for preparing a hot work die steel material, the specific preparation steps are:
[0057] Step 1. Initial refining: put iron and carbon into an intermediate frequency induction furnace for smelting according to the ratio of raw materials to obtain base molten steel, and then transfer the base molten steel into a vacuum refining furnace for vacuum refining to prepare refined molten steel;
[0058] Step 2. Mixing: transfer the refined molten steel into the intermediate frequency induction furnace, then add chromium, vanadium, tungsten, molybdenum, copper, manganese, nickel, silicon to the intermediate frequency induction furnace in sequence according to the ratio of raw materials, melt and mix them , t...
PUM
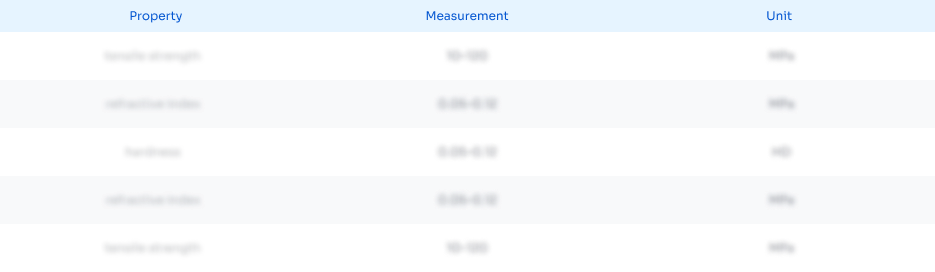
Abstract
Description
Claims
Application Information

- R&D
- Intellectual Property
- Life Sciences
- Materials
- Tech Scout
- Unparalleled Data Quality
- Higher Quality Content
- 60% Fewer Hallucinations
Browse by: Latest US Patents, China's latest patents, Technical Efficacy Thesaurus, Application Domain, Technology Topic, Popular Technical Reports.
© 2025 PatSnap. All rights reserved.Legal|Privacy policy|Modern Slavery Act Transparency Statement|Sitemap|About US| Contact US: help@patsnap.com