Separation device and separation method for preventing coking at bottom of catalytic depropanization tower
A technology of depropanizer tower and depropanizer tower, which is applied in the field of separation device to prevent coking at the bottom of catalytic depropanizer tower, and can solve problems such as increased production and operation costs
- Summary
- Abstract
- Description
- Claims
- Application Information
AI Technical Summary
Problems solved by technology
Method used
Image
Examples
Embodiment 1
[0048] In this embodiment, the depropanizer 1 has 30 theoretical plates, the operating pressure at the top of the tower is 0.85 MPag, the temperature at the top of the tower is 16°C, and the temperature at the bottom of the tower is 74.3°C. The inlet line 2 is located above the tray 10 of the depropanizer 1 . The fuel gas is discharged directly to the flare. The tower top condensing mechanism 4 adopts mode 1, the gaseous phase material at the tower top is condensed by the condenser 404, and the condenser 404 uses 7°C refrigerant water as a cooling source. The bottom reboiler 10 uses 90°C hot water as a heat source.
[0049] The separation method includes the following steps:
[0050] The material from the upstream device enters the depropanizer 1 through the side line inlet pipeline 2; the gas phase material from the top of the depropanizer 1 is cooled by the top condenser 404 to form a condensate and enters the top reflux tank 5, and the condensate is pressurized by a pump ...
Embodiment 2
[0052] In this embodiment, the depropanizer 1 has 30 theoretical plates, the operating pressure at the top of the tower is 0.6 MPag, the temperature at the top of the tower is 6.5° C., and the temperature at the bottom of the tower is 63.3° C. The side inlet line 2 is located above the tray 10 of the depropanizer 1 . The tower top condensing mechanism 4 adopts the second method, the gas phase material at the top of the tower is pressurized to 1.7MPag by the first tower top gas booster 405, and then enters the cooler 406, and the cooler 406 is cooled by an air cooler. The bottom reboiler 10 uses 85°C hot water as a heat source.
[0053] The separation method includes the following steps:
[0054] The material from the upstream device enters the depropanizer 1 through the side line inlet pipeline 2; the gas phase material coming out of the top of the depropanizer 1 is pressurized by the first tower top gas booster 405, and then enters the cooler 406, and the air cooler is used ...
Embodiment 3
[0056] In this example, the depropanizer 1 has 30 theoretical plates, the operating pressure at the top of the tower is 0.65 MPag, the temperature at the top of the tower is 8.8°C, and the temperature at the bottom of the tower is 65.2°C. The side inlet line 2 is located at the 10th floor of the tray. The tower top condensing mechanism 4 adopts the third method. After the tower top gas phase is pressurized to 2.85 MPag by the second tower top gas booster 407, it enters the tower bottom reboiler 10, exchanges heat with the tower bottom material, and then passes through the tower top gas. After the cooler 408 is condensed, all condensate is formed and enters the top reflux tank 5 . The bottom reboiler 10 does not require an external heat source.
[0057] The separation method includes the following steps:
[0058] The material from the upstream device enters the depropanizer 1 through the side line inlet pipeline 2; the gas phase material coming out of the top of the depropani...
PUM
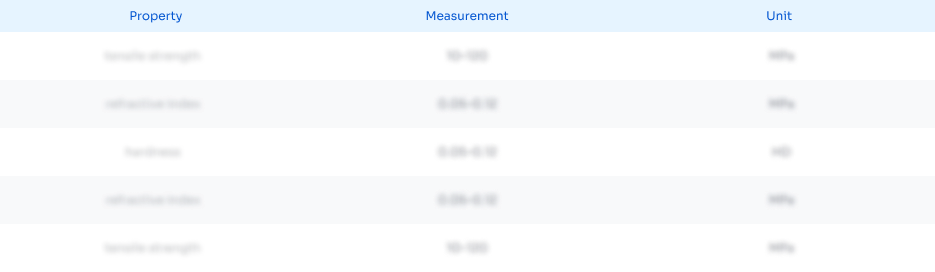
Abstract
Description
Claims
Application Information

- R&D
- Intellectual Property
- Life Sciences
- Materials
- Tech Scout
- Unparalleled Data Quality
- Higher Quality Content
- 60% Fewer Hallucinations
Browse by: Latest US Patents, China's latest patents, Technical Efficacy Thesaurus, Application Domain, Technology Topic, Popular Technical Reports.
© 2025 PatSnap. All rights reserved.Legal|Privacy policy|Modern Slavery Act Transparency Statement|Sitemap|About US| Contact US: help@patsnap.com