On-orbit spacecraft flywheel fault detection method based on kernel principal component analysis
A nuclear principal component analysis and fault detection technology, which is applied in the direction of instruments, electrical testing/monitoring, testing/monitoring control systems, etc., can solve the lack of independent research and judgment of unknown faults, the lack of online analysis capabilities of massive data, and the deep extraction of fault data Insufficient and other problems, to achieve the effect of intuitive display of detection indicators, improved accuracy, and strong scalability
- Summary
- Abstract
- Description
- Claims
- Application Information
AI Technical Summary
Problems solved by technology
Method used
Image
Examples
Embodiment Construction
[0103] The implementation process of the present invention will be described in detail below by taking a certain type of spacecraft that uses three orthogonal flywheel sets as the actuator as an example.
[0104] The flywheel fault modeling formula is:
[0105] T m (t f ) = e mf T mt (t f )+f a (twenty one)
[0106] t f is the fault time, T m (t f ) is the actual electromagnetic torque generated by the flywheel motor at this time, e mf ∈[0,1] is the current multiplicative effective coefficient of the flywheel, T mt (t f ) for t f The electromagnetic torque that the flywheel motor should produce under normal conditions at time, f a is its current additive bias.
[0107] The common gain fault, deviation fault and idling fault of the flywheel are selected for simulation, and the faults are correspondingly set on the flywheel 1, 2, and 3. The specific fault parameters are shown in Table 1:
[0108] Table 1 Flywheel failure parameters
[0109]
[0110] 1, the ap...
PUM
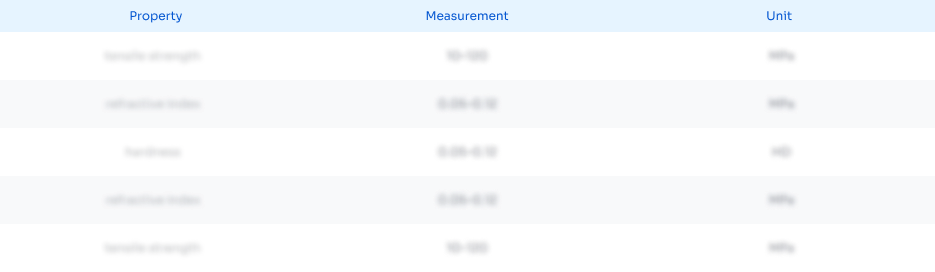
Abstract
Description
Claims
Application Information

- R&D Engineer
- R&D Manager
- IP Professional
- Industry Leading Data Capabilities
- Powerful AI technology
- Patent DNA Extraction
Browse by: Latest US Patents, China's latest patents, Technical Efficacy Thesaurus, Application Domain, Technology Topic, Popular Technical Reports.
© 2024 PatSnap. All rights reserved.Legal|Privacy policy|Modern Slavery Act Transparency Statement|Sitemap|About US| Contact US: help@patsnap.com