High-entropy stable rare earth tantalate/niobate ceramic and preparation method thereof
A technology of niobate and tantalate, which is applied in the field of high-entropy stable rare earth tantalate/niobate ceramics and its preparation, can solve the problems of low thermal expansion coefficient, insufficient thermal radiation resistance, and poor fracture toughness, and achieve Improves purity, inhibits grain growth and precipitated phase generation, and has the effect of high density
- Summary
- Abstract
- Description
- Claims
- Application Information
AI Technical Summary
Problems solved by technology
Method used
Image
Examples
preparation example Construction
[0034] against the current A 3 BO 7 type rare earth tantalum / niobate and A 2 B 2 o 7 Type rare earth zirconium / titanium / tin / hafnate ceramics have problems such as low coefficient of thermal expansion, poor fracture toughness and insufficient thermal radiation resistance. The present invention provides a high-entropy stable rare earth tantalate / niobate ceramic The preparation method comprises the steps of:
[0035] RE 2 o 3 (RE is a rare earth element), tantalum oxide Ta 2 o 5 , niobium oxide Nb 2 o 5 and MO 2 (M=Sn, Ti, Zr, Hf) oxide (M is selected from at least one of Sn, Ti, Zr, Hf) as raw material, with A 3 BO 7 Type rare earth tantalum / niobate RE 3 Ta 1-x Nb x o 7 Ceramic as the matrix, adding three or more different types of MO with the same content (or molar ratio) 2 The oxide can replace the rare earth and tantalum / niobium elements at the A and B positions in equal quantities, and maintain the electronegativity of the crystal lattice to obtain a compoun...
Embodiment 1
[0053] Preparation A 3 BO 7 Type Gd 2.6 Ta 0.3 Nb 0.3 Ti 0.2 Zr 0.2 f 0.2 sn 0.2 o 7 High-entropy ceramics, the specific steps are as follows:
[0054] Raw material Gd 2 o 3 、 Ta 2 o 5 , Nb 2 o 5 and MO 2 (M=Sn, Ti, Zr, Hf) were weighed according to the stoichiometric ratio, and then placed in a high-temperature furnace at 1200°C for 5 hours to remove organic impurities contained in the raw material powder and reduce the reactivity of the raw material powder; Then the raw material powder is cooled to room temperature, and the cooled raw material powder, alcohol and zirconia ball are placed in a ball mill tank according to the mass ratio of 1:2:3 for ball mill mixing, and the speed of ball milling is 600 rpm , the ball milling time was 36 hours, and then the uniformly mixed powder was kept at 100° C. for 5 hours for drying treatment, and finally sieved with 400 meshes to obtain a fine powder. Weigh about 2.0g of the sieved powder and place it in a graphite grin...
Embodiment 2
[0056] Preparation A 2 B 2 o 7 Type Yb 2.5 Ta 0.25 Nb 0.25 Ti 0.25 Zr 0.25 f 0.25 sn 0.25 o 7 ,Specific steps are as follows:
[0057] Raw material Yb 2 o 3 、 Ta 2 o 5 , Nb2 o 5 and MO 2 (M=Sn, Ti, Zr, Hf) were weighed according to the stoichiometric ratio, and then placed in a high-temperature furnace at 800°C for 2 hours to remove organic impurities contained in the raw material powder and reduce the reactivity of the raw material powder; Then the raw material powder is cooled to room temperature, and the cooled raw material powder, alcohol and zirconia ball are placed in a ball mill tank according to the mass ratio of 1:2:2 for ball mill mixing, and the speed of ball milling is 300 rpm , the ball milling time is 12 hours, and then the uniformly mixed powder is kept at 90° C. for 8 hours for drying treatment, and finally sieved with 200 meshes to obtain a fine powder. Weigh about 2.0g of the sieved powder and place it in a graphite grinding tool for developm...
PUM
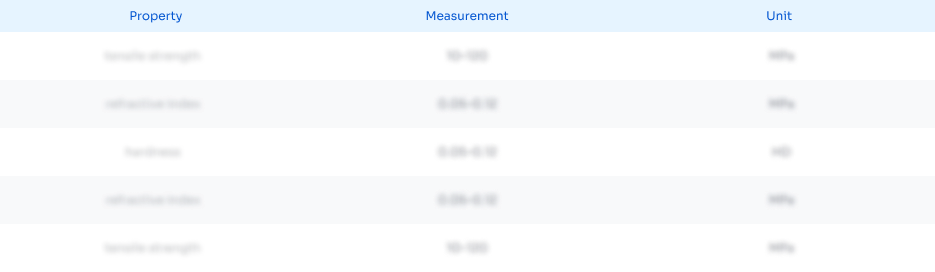
Abstract
Description
Claims
Application Information

- R&D
- Intellectual Property
- Life Sciences
- Materials
- Tech Scout
- Unparalleled Data Quality
- Higher Quality Content
- 60% Fewer Hallucinations
Browse by: Latest US Patents, China's latest patents, Technical Efficacy Thesaurus, Application Domain, Technology Topic, Popular Technical Reports.
© 2025 PatSnap. All rights reserved.Legal|Privacy policy|Modern Slavery Act Transparency Statement|Sitemap|About US| Contact US: help@patsnap.com