A kind of ceramic material crushing equipment and ceramic material processing technology
A technology of ceramic materials and crushing equipment, which is applied in clay processing equipment, clay preparation equipment, chemical instruments and methods, etc., can solve the problems of insufficient particle crushing, insufficient grinding, and easy occurrence of heat, etc., and achieves convenient replacement and maintenance , Improve the efficiency of replacement and save costs
- Summary
- Abstract
- Description
- Claims
- Application Information
AI Technical Summary
Problems solved by technology
Method used
Image
Examples
Embodiment 1
[0044] Example 1: When working, first pour the material to be pulverized into the box 1 through the feeding port 11, and start the work of the rotary motor 2, at this time, the pulverizing knife 4 outside the rotary motor 2 pulverizes the material to be pulverized At the same time, the stirring plate 6 on the outer side of the installation column 3 located under the crushing knife 4 stirs the material, so that the material at the bottom and the material above can be alternately replaced during the crushing process, so as to avoid the material at the bottom that cannot be crushed, resulting in In the case of uneven pulverization, when the material meets the requirements of the pulverization size during the pulverization process, the side enters the lower end area of the box body 1 through the filter holes on the filter plate 71, and stops the pulverizing work with the pulverizing knife 4. To avoid that the particles are smaller due to excessive crushing, and the materials that...
Embodiment 2
[0045] Embodiment 2: After a long period of continuous operation, the external temperature of the pulverizing knife 4 is higher due to friction between the pulverizing knife 4 and the material, which affects the subsequent pulverizing work of the pulverizing knife 4. When the continuous working time of the rotary motor 2 reaches a micrometer When the preset value in the data processor 5 is set, the micro data processor 5 sends the time to stop working to the rotary motor 2, and sends an instruction to start the work to the cooling pipe 42 in the pulverizing knife 4, and the pulverizing knife 4 stops at this time. The crushing work is performed, and the cooling pipe 42 in the crushing knife 4 cools the crushing knife 4. During the cooling process of the cooling pipe 42, the cold air of the cooling pipe 42 is transmitted to the heat dissipation plate 431 through the connecting pipe 43, and passes through the heat dissipation plate 431. The work of cooling and heat dissipation is ...
Embodiment 3
[0046] Embodiment 3: After using for a period of time, the box door of the box body 1 can be opened to repair and replace the crushing knife 4 and the filter plate 71. During the maintenance, the installation column 3 and the connecting seat 21 can be rotated first, and at the same time Release the connection between the first limit buckle 32 and the fixing buckle 31, complete the disassembly between the installation column 3 and the connecting seat 21, and repair the crushing knife 4. When it is found that the crushing blade 4 needs to be replaced, it is only necessary to turn the installation head 44, the installation head 44 is separated from the threaded groove 331, the crushing knife 4 to be replaced or repaired is removed, and the new crushing knife 4 is installed through the installation head 44 and the threaded groove 331 to complete the crushing knife 4 and the installation column. The installation and fixation between 3 and 3, in addition, the abdication groove 441 on...
PUM
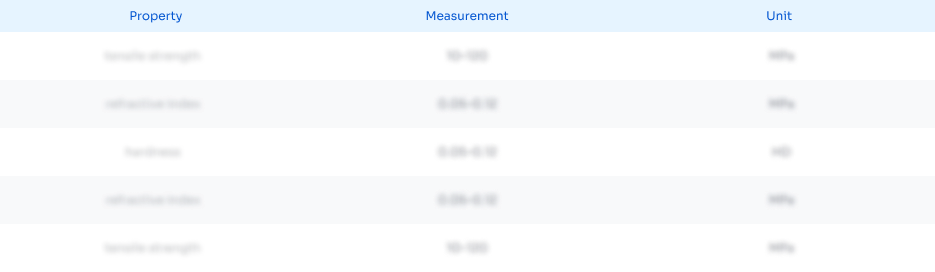
Abstract
Description
Claims
Application Information

- R&D
- Intellectual Property
- Life Sciences
- Materials
- Tech Scout
- Unparalleled Data Quality
- Higher Quality Content
- 60% Fewer Hallucinations
Browse by: Latest US Patents, China's latest patents, Technical Efficacy Thesaurus, Application Domain, Technology Topic, Popular Technical Reports.
© 2025 PatSnap. All rights reserved.Legal|Privacy policy|Modern Slavery Act Transparency Statement|Sitemap|About US| Contact US: help@patsnap.com