Extrusion and compression molding method for fiber reinforced plastic part and capable of achieving series blasting synergetic blending
A technology of fiber-reinforced plastics and compression molding, which is applied in the field of injection molding processing. It can solve the problems of difficulty in reconciling the length of fiber dispersion and retention, and achieve the effects of shortening the injection molding cycle and thermomechanical history, reducing pressure, and reducing the degree of fracture.
- Summary
- Abstract
- Description
- Claims
- Application Information
AI Technical Summary
Problems solved by technology
Method used
Image
Examples
Embodiment Construction
[0022] The present invention will be further described below in conjunction with drawings and embodiments.
[0023] In this embodiment, the equipment used in the process of series blasting synergistic blending and extrusion injection mold filling is a twin-shaft eccentric rotor extruder, such as figure 1 As shown, the twin-shaft eccentric rotor extruder is mainly composed of the first feed port, the second feed port, two eccentric rotors, the stator, the heater, the exhaust port and the self-locking nozzle, wherein the first feed port , The second feed port and the exhaust port are connected with the inner cavity of the stator, and the first feed port, the second feed port and the exhaust port are distributed sequentially along the direction of material travel; the heater is installed on the outer wall of the stator, 2 Two eccentric rotors are arranged parallel to the inner cavity of the stator, the self-locking nozzle is installed at the outlet of the stator, and the self-loc...
PUM
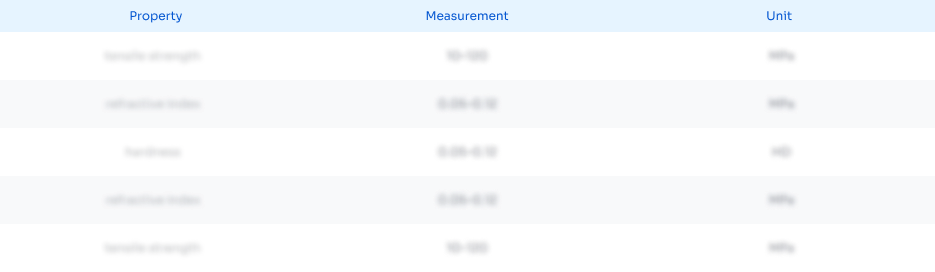
Abstract
Description
Claims
Application Information

- R&D
- Intellectual Property
- Life Sciences
- Materials
- Tech Scout
- Unparalleled Data Quality
- Higher Quality Content
- 60% Fewer Hallucinations
Browse by: Latest US Patents, China's latest patents, Technical Efficacy Thesaurus, Application Domain, Technology Topic, Popular Technical Reports.
© 2025 PatSnap. All rights reserved.Legal|Privacy policy|Modern Slavery Act Transparency Statement|Sitemap|About US| Contact US: help@patsnap.com