Method for recycling regenerated sodium ion battery cathode material from waste lithium cobalt oxide battery cathode material
A sodium-ion battery and battery positive electrode technology, which is applied in the field of recycling waste lithium cobalt oxide battery positive electrode materials to regenerate metal sulfide negative electrode materials for sodium-ion batteries, can solve the problems of long and complicated processes, and achieve the reduction of recycling processes, simple methods, and The effect of excellent electrochemical performance
- Summary
- Abstract
- Description
- Claims
- Application Information
AI Technical Summary
Problems solved by technology
Method used
Image
Examples
Embodiment 1
[0023] (1) Take 20 g of spent lithium cobaltate positive electrode powder and put it into a ball mill tank, put it into a ball mill, and grind it for 9 hours at a speed of 600 r / min to obtain a uniformly mixed powder material.
[0024] (2) Take 5g of sublimated sulfur and 5g of waste electrode materials and put them into different small porcelain boats, respectively, and place them in the upstream and middle parts of the tube furnace tube respectively. 2 Under the atmosphere, the temperature was raised to 700°C at a heating rate of 5°C / min and kept for 2h.
[0025] (3) Put the obtained composite material into a beaker, add 600mL deionized water at the same time, extract Li, and after ultrasonic treatment for 30min, perform suction filtration, and dry the filter cake in an oven at 120°C to obtain metal sulfide materials, phase test results such as figure 1 shown, for CoS 2 And the composite material of C can be directly used as the negative electrode material of sodium ion ba...
Embodiment 2
[0028] (1) Take 20 g of spent lithium cobaltate positive electrode powder and put it into a ball mill tank, put it into a ball mill, and grind it for 9 hours at a speed of 300 r / min to obtain a uniformly mixed powder material.
[0029] (2) Take 5g of sublimated sulfur and 5g of waste electrode materials and put them into different small porcelain boats, respectively, and place them in the upstream and middle parts of the tube furnace tube respectively. 2 Under the atmosphere, the temperature was raised to 600°C at a heating rate of 5°C / min and kept for 2h.
[0030] (3) Put the obtained composite material into a beaker, add 300mL deionized water at the same time, extract Li, and after ultrasonic treatment for 30min, perform suction filtration, and dry the filter cake in an oven at 120°C to obtain metal sulfide material.
PUM
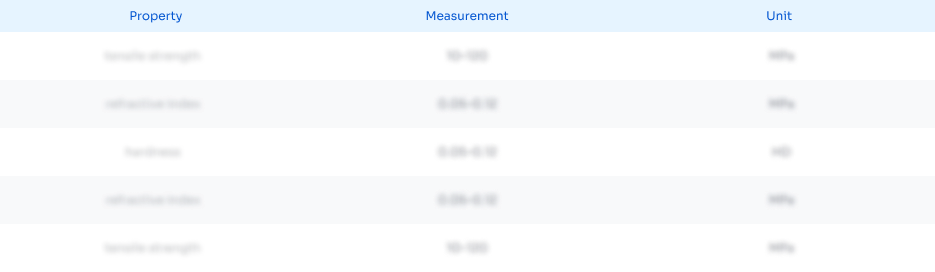
Abstract
Description
Claims
Application Information

- R&D Engineer
- R&D Manager
- IP Professional
- Industry Leading Data Capabilities
- Powerful AI technology
- Patent DNA Extraction
Browse by: Latest US Patents, China's latest patents, Technical Efficacy Thesaurus, Application Domain, Technology Topic, Popular Technical Reports.
© 2024 PatSnap. All rights reserved.Legal|Privacy policy|Modern Slavery Act Transparency Statement|Sitemap|About US| Contact US: help@patsnap.com