Method for co-extraction-selective reverse extraction separation of vanadium and chromium from solution containing vanadium and chromium
A selective, solution-based technology, applied in the direction of improving process efficiency, etc., can solve the problems of difficult preparation of pure substances, high impurity entrainment, complicated process, etc., and achieve good effect, high recovery rate of vanadium chromium, and short process.
- Summary
- Abstract
- Description
- Claims
- Application Information
AI Technical Summary
Problems solved by technology
Method used
Image
Examples
Embodiment 1
[0056] Get 5L and contain V 30g / L, the high chromium vanadium slag sodiumization roasting water leachate (pH is 13.5) that contains V 30g / L, Cr 32g / L, add sulfuric acid to adjust leachate pH value to be 10.5, then make solution and composition into 20% methyl trioctyl Extractant (in formula 1, R 1 ~R 3 is n-octyl; R 4 for CH 3 ;A - for Cl - ) + 30% 2-octanol + 50% aviation kerosene (volume percentage) mixed organic phase, and carried out 14 stages of countercurrent extraction under the condition that the flow ratio was 8:1 to obtain the raffinate and the organic phase O1 loaded with vanadium chromium. During the extraction process, the extraction rate of chromium is 99.9%, and the extraction rate of vanadium is 99.9%.
[0057] After the loaded organic phase O1 was washed, 3-stage countercurrent back extraction was carried out with 15 mol / L sodium hydroxide solution, and the contact concentration of alkali was 4 mol / L to obtain the vanadium-containing back extraction solut...
Embodiment 2
[0066] Get 5L and contain V1.0g / L, Cr 1.5g / L vanadium slag sodiumization roasting water soaking liquid acidic ammonium salt precipitation vanadium mother liquor (pH is 2.5), adds sodium hydroxide and regulates leach solution pH value is 6.0, then solution and Composition is 50% methyl trioctyl extractant (in formula 1, R 1 ~R 3 is n-octyl; R 4 for CH 3 ;A - for CO 3 2- )+50% sulfonated kerosene (volume percent) mixed organic phase, and carried out three-stage countercurrent extraction under the condition that the flow ratio was 1:10, to obtain the raffinate and the organic phase O1 loaded with vanadium and chromium. During the extraction process, the extraction rate of chromium is 99.8%, and the extraction rate of vanadium is 99.7%.
[0067] After the loaded organic phase O1 was washed, 10-stage countercurrent back extraction was carried out with 6 mol / L potassium hydroxide solution, and the contact concentration of alkali was 3 mol / L to obtain vanadium-containing stripp...
Embodiment 3
[0079] Get 5L containing V 20g / L, the vanadium-chromium solid waste residue sodiumization roasting water leaching solution (pH is 12.0) that the phosphorous chemical industry enterprise that Cr 1.5g / L produces, adds hydrochloric acid and regulates the leaching solution pH value to be 8.0, then solution and composition is 5% methyltrinonyl extractant (in formula 1, R 1 ~R3 is n-nonyl, R 4 for CH 3 ;A - for CO 3 2- )+10% tridecyl alcohol+85% No. 200 solvent oil (volume percentage) mixed with the organic phase, and carried out 10 stages of countercurrent extraction under the condition that the flow ratio is 1:5, to obtain the raffinate and the organic phase loaded with vanadium chromium O1. After the loaded organic phase O1 was washed, 8-stage countercurrent back extraction was carried out with 6 mol / L sodium hydroxide solution, and the contact concentration of alkali was 3.5 mol / L to obtain vanadium-containing stripping liquid L1 and negative chromium organic phase O2. The...
PUM
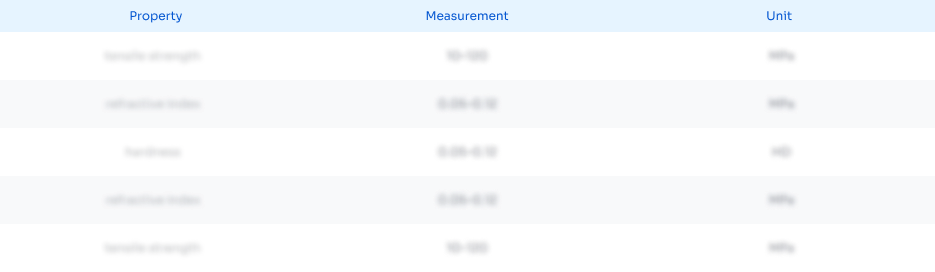
Abstract
Description
Claims
Application Information

- R&D
- Intellectual Property
- Life Sciences
- Materials
- Tech Scout
- Unparalleled Data Quality
- Higher Quality Content
- 60% Fewer Hallucinations
Browse by: Latest US Patents, China's latest patents, Technical Efficacy Thesaurus, Application Domain, Technology Topic, Popular Technical Reports.
© 2025 PatSnap. All rights reserved.Legal|Privacy policy|Modern Slavery Act Transparency Statement|Sitemap|About US| Contact US: help@patsnap.com