High-density ceramic material as well as preparation method and application thereof
A ceramic material and density technology, which is applied in the field of high-density ceramic materials and its preparation, can solve the problems of low density of products, obstacles to the application and development of thermal protection of aerospace vehicles, and high sintering temperature
- Summary
- Abstract
- Description
- Claims
- Application Information
AI Technical Summary
Problems solved by technology
Method used
Image
Examples
preparation example Construction
[0030] The present invention provides a preparation method for the high-density ceramic material described in the above technical solution, comprising the following steps:
[0031] Mixing lanthanum source, magnesium source, transition metal oxide, iron source, cobalt source, nickel source and aluminum source, carrying out stage-by-stage pressure-holding molding to obtain a green body; the lanthanum source, magnesium source, transition metal oxide, iron The molar ratio of lanthanum element, magnesium element, transition metal element, iron element, cobalt element, nickel element and aluminum element in source, cobalt source, nickel source and aluminum source is 1:(0.4-x):x:0.2:0.2: 0.2:11, 0<x≤0.2; the transition metal oxide includes copper oxide or zinc oxide;
[0032] Sintering the green body without pressure to obtain a high-emissivity high-entropy ceramic material;
[0033] The step-by-step pressure-holding molding process includes: the first stage: the molding pressure is 2...
Embodiment 1
[0050] La 2 o 3 Powder (average particle size 0.5 μm, purity ≥ 99.9%), FeO powder (average particle size 0.5 μm, purity ≥ 99.9%), CoO powder (average particle size 0.5 μm, purity ≥ 99.9%), NiO powder (average particle size 0.5μm, purity ≥ 99.9%), ZnO powder (average particle size 0.5μm, purity ≥ 99.9%), Al 2 o 3 Powder (average particle size 0.5 μm, purity ≥ 99.9%) and MgO powder (average particle size 0.5 μm, purity ≥ 99.9%) according to La (Mg 0.2 Zn 0.2 Fe 0.2 co 0.2 Ni 0.2 ) Al 11 o 19 The stoichiometric ratio is batched, where La 2 o 3 , FeO powder, CoO powder, NiO powder, ZnO powder, Al 2 o 3 The molar ratio of the powder and the MgO powder is respectively 1:0.4:0.4:0.4:0.4:11:0.4, and the obtained mixture is mixed with absolute ethanol to carry out wet ball milling, the ball milling speed is 280rpm, and the ball milling time is 18h, dark brown mixed powder was obtained;
[0051] Put the dark brown mixed powder into a stainless steel mould, first place the ...
Embodiment 2
[0054] La 2 o 3 Powder (average particle size 0.5 μm, purity ≥ 99.9%), FeO powder (average particle size 0.5 μm, purity ≥ 99.9%), CoO powder (average particle size 0.5 μm, purity ≥ 99.9%), NiO powder (average particle size 0.5μm, purity ≥ 99.9%), CuO powder (average particle size 0.5μm, purity ≥ 99.9%), Al 2 o 3 Powder (average particle size 0.5 μm, purity ≥ 99.9%) and MgO powder (average particle size 0.5 μm, purity ≥ 99.9%) according to La (Mg 0.2 Cu 0.2 Fe 0.2 co 0.2 Ni 0.2 ) Al 11 o 19 The stoichiometric ratio is batched, where La 2 o 3 , FeO powder, CoO powder, NiO powder, CuO powder, Al 2 o 3 The molar ratios of the powder and the MgO powder are respectively 1:0.4:0.4:0.4:0.4:11:0.4, the resulting mixture is mixed with absolute ethanol, and wet ball milled, the ball milling speed is 250rpm, and the ball milling time is 24h, Obtain dark brown mixed powder;
[0055] Place the dark brown mixed powder in the forward direction under the pressure of 3.2MPa and ho...
PUM
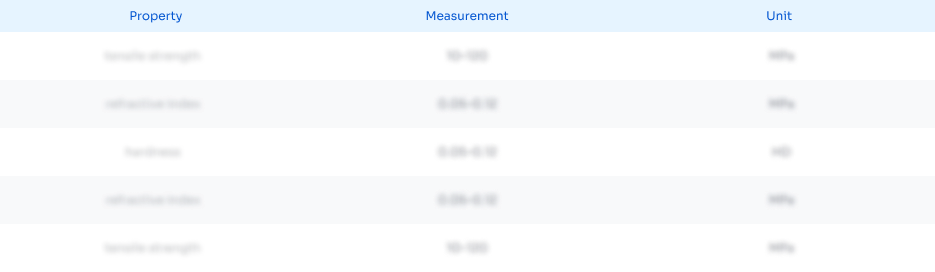
Abstract
Description
Claims
Application Information

- R&D
- Intellectual Property
- Life Sciences
- Materials
- Tech Scout
- Unparalleled Data Quality
- Higher Quality Content
- 60% Fewer Hallucinations
Browse by: Latest US Patents, China's latest patents, Technical Efficacy Thesaurus, Application Domain, Technology Topic, Popular Technical Reports.
© 2025 PatSnap. All rights reserved.Legal|Privacy policy|Modern Slavery Act Transparency Statement|Sitemap|About US| Contact US: help@patsnap.com