Method for improving papermaking drainage performance by adopting microfibrillated fibers
A technology of microfibrillation and performance, which is applied in the post-treatment modification of cellulose pulp, the addition of non-fibrous pulp, and the treatment of fiber raw materials. It can solve problems such as water drainage problems, reduce dosage, increase filler content, and improve drainage. and the effect of retaining performance
- Summary
- Abstract
- Description
- Claims
- Application Information
AI Technical Summary
Problems solved by technology
Method used
Image
Examples
Embodiment 1
[0020] (1) Fully decompress the hardwood chemical pulp in a beater, then adjust the fiber solid content to 3.5% after decompression, and then grind it on a grinder to prepare microfibrillated cellulose, and select the obtained grinding gap as -2um The median particle size of microfibrillated cellulose is 21 μm.
[0021] (2) Mix bleached kraft softwood pulp (beating degree 40~45°SR) and bleached kraft hardwood pulp (beating degree 37~42°SR) in a mass ratio of 30:70, and add 5% micro Fibrillated cellulose, 50% GCC, 1% cationic starch, 0.2% AKD sizing agent and 0.03% cationic polyacrylamide retention aid, mix well, add water to dilute to a pulp concentration of 0.5%, and use standard paper sheet forming Machine for papermaking, paper weight 60g / m 2 . The water filtration performance of paper material is as attached figure 1 As shown in Table 1, the paper properties are shown in Table 2.
[0022] The water filtration performance of the paper material is expressed by the suctio...
Embodiment 2
[0024] (1) Fully decompose the hardwood chemical pulp in a beater, then adjust the fiber solid content to 3.0% after decompression, add 0.5% polydiallyl dimethyl ammonium chloride to this suspension and mix well uniform. The uniformly mixed pulp fiber suspension was ground on a grinder to prepare microfibrillated cellulose, and the median particle size of the obtained microfibrillated cellulose was 16.3um when the grinding gap was selected to be -2um.
[0025] (2) After fully mixing the ground microfibrillated cellulose and GCC, continue to grind in the grinder until the formation of microfibrillated fibers and filler composites. The amount of microfibrillated cellulose is calculated as 5% dry GCC. %.
[0026] (3) Mix bleached kraft softwood pulp (beating degree 40~45°SR) and bleached kraft hardwood pulp (beating degree 37~42°SR) in a mass ratio of 30:70, and add 55% micro Fibrillated fiber-filler compound, 1% cationic starch, 0.2% AKD sizing agent and 0.03% cationic polyacr...
Embodiment 3
[0028] (1) The bleached bamboo pulp is fully decomposed in a beater, and then the fiber solid content is adjusted to 4.5% after decompression, and 0.25% polyamine is added to the suspension and fully mixed. The uniformly mixed pulp fiber suspension was ground on a grinder to prepare microfibrillated cellulose, and the median particle size of the obtained microfibrillated cellulose was 68.9um when the grinding gap was selected to be -5um.
[0029] (2) After fully mixing the ground microfibrillated cellulose and china clay, continue grinding in the grinder until the formation of microfibrillated fibers and filler composites, the amount of microfibrillated cellulose is 10% based on the amount of dry china clay %.
[0030] (3) Mix bleached kraft softwood pulp (beating degree 40~45°SR) and bleached kraft hardwood pulp (beating degree 37~42°SR) in a mass ratio of 30:70, and add 55% micro Fibrillated fiber-filler compound, 1% cationic starch, 0.2% AKD sizing agent and 0.03% cationic...
PUM
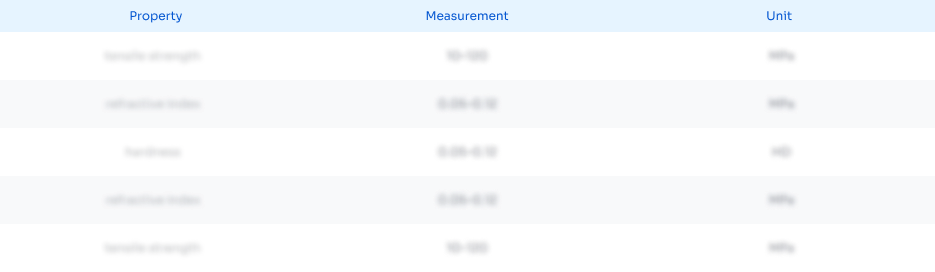
Abstract
Description
Claims
Application Information

- R&D Engineer
- R&D Manager
- IP Professional
- Industry Leading Data Capabilities
- Powerful AI technology
- Patent DNA Extraction
Browse by: Latest US Patents, China's latest patents, Technical Efficacy Thesaurus, Application Domain, Technology Topic, Popular Technical Reports.
© 2024 PatSnap. All rights reserved.Legal|Privacy policy|Modern Slavery Act Transparency Statement|Sitemap|About US| Contact US: help@patsnap.com