Preparation method of carbon defect type carbon nitride material for photocatalytic nitrogen fixation
A carbon nitride and carbon defect technology, which is applied in the field of preparation of carbon-defective carbon nitride materials, can solve the problems of low dispersion, high recombination rate, low electrical conductivity, etc., and achieves reduced recombination rate, short production cycle, The effect of reducing production costs
- Summary
- Abstract
- Description
- Claims
- Application Information
AI Technical Summary
Problems solved by technology
Method used
Image
Examples
Embodiment 1
[0037] 1. Put 20g of urea in a 100ml covered quartz crucible and put it into a muffle furnace for calcination. The calcination temperature is 550°C, the holding time is 4 hours, and the heating rate is 5°C / min;
[0038] 2. Grind for 30 minutes to obtain finely divided carbon nitride powder;
[0039] 3. The second calcination: spread the above-mentioned carbon nitride evenly in the porcelain boat, the thickness should not exceed 2mm, put it into the muffle furnace for calcination, the calcination temperature is 520°C, the holding time is 2 hours, and the heating rate is 5°C / min;
[0040] 4. The third calcination: spread the above-mentioned carbon nitride evenly in the porcelain boat, the thickness should not exceed 2mm, put it into the muffle furnace for calcination, the calcination temperature is 520°C, the holding time is 2 hours, and the heating rate is 5°C / min.
Embodiment 2
[0042] 1. Put 20g of urea in a 100ml covered quartz crucible and put it into a muffle furnace for calcination. The calcination temperature is 530°C, the holding time is 2 hours, and the heating rate is 2°C / min;
[0043] 2. Grind for 30 minutes to obtain finely divided carbon nitride powder;
[0044] 3. The second calcination: spread the above-mentioned carbon nitride evenly in the porcelain boat, the thickness should not exceed 2mm, put it into the muffle furnace for calcination, the calcination temperature is 550°C, the holding time is 4 hours, and the heating rate is 2°C / min;
[0045]4. The third calcination: spread the above-mentioned carbon nitride evenly in the porcelain boat, the thickness should not exceed 2mm, put it into the muffle furnace for calcination, the calcination temperature is 550°C, the holding time is 4 hours, and the heating rate is 2°C / min.
Embodiment 3
[0047] 1. Put 20g of urea in a 100ml covered quartz crucible and put it into a muffle furnace for calcination. The calcination temperature is 520°C, the holding time is 3 hours, and the heating rate is 3°C / min;
[0048] 2. Grind for 30 minutes to obtain finely divided carbon nitride powder;
[0049] 3. The second calcination: spread the above-mentioned carbon nitride evenly in the porcelain boat, the thickness should not exceed 2mm, put it into the muffle furnace for calcination, the calcination temperature is 530°C, the holding time is 3 hours, and the heating rate is 3°C / min;
[0050] 4. The third calcination: spread the above-mentioned carbon nitride evenly in the porcelain boat, the thickness should not exceed 2mm, put it into the muffle furnace for calcination, the calcination temperature is 530°C, the holding time is 3 hours, and the heating rate is 3°C / min.
[0051] Such as figure 1 Shown, g-C 3 N 4 For bulk carbon nitride, g-C 3 N 4 -V is carbon-deficient carb...
PUM
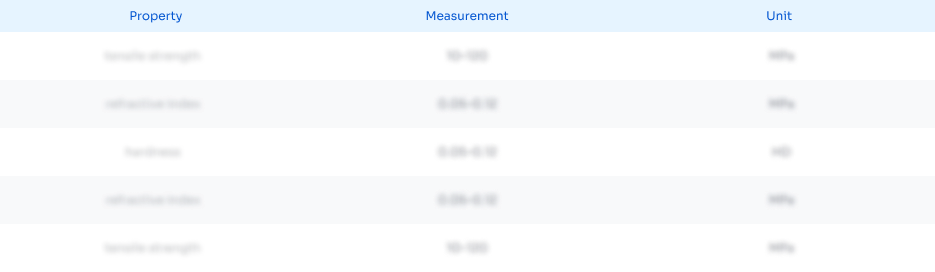
Abstract
Description
Claims
Application Information

- R&D
- Intellectual Property
- Life Sciences
- Materials
- Tech Scout
- Unparalleled Data Quality
- Higher Quality Content
- 60% Fewer Hallucinations
Browse by: Latest US Patents, China's latest patents, Technical Efficacy Thesaurus, Application Domain, Technology Topic, Popular Technical Reports.
© 2025 PatSnap. All rights reserved.Legal|Privacy policy|Modern Slavery Act Transparency Statement|Sitemap|About US| Contact US: help@patsnap.com