Sulfur transfer agent with surface rich in alkaline sites and preparation method thereof
A technology of sulfur transfer agent and site, applied in the direction of separation methods, chemical instruments and methods, and other chemical processes, can solve the problems of high wear index of additives, unsatisfactory desulfurization effect, high specific surface area, etc., and achieve good wear index, The effect of additives with many basic sites and large specific surface area
- Summary
- Abstract
- Description
- Claims
- Application Information
AI Technical Summary
Problems solved by technology
Method used
Image
Examples
Embodiment 1
[0052] Add 0.589kg of pseudo-boehmite (dry basis) into 7.5kg of water, add 0.35kg of formic acid under stirring conditions (130 rpm), and mark it as slurry A.
[0053] 0.21 kg of magnesium oxide (dry basis) was dispersed in 0.6 kg of water, marked as slurry B.
[0054] 0.54kg cerium chloride solution (containing 18% CeO 2 ) into 0.1 kg of water, marked as liquid C.
[0055] 48g ammonium metavanadate (containing 36.6g V 2 o 5 ) was added to 0.3kg of water, and 0.1kg of formic acid was added under stirring conditions (130 rpm), marked as liquid D.
[0056] Put A, B, C, and D into the colloid mill (rotating speed 2900 rpm, processing precision 2-40 microns) in sequence for 10 minutes, and then spray molding. Baked at 700°C for 2h, marked as S1.
[0057] The element composition, specific surface area, wear index and particle size distribution of S1 are shown in Table 1 and Table 2. CO of S1 2 adsorption infrared see figure 2 . S1 and H 2 Reduction of regenerated S1 to S...
Embodiment 2
[0059] Add 0.589kg of pseudo-boehmite (dry basis) into 7.5kg of water, add 0.35kg of formic acid under stirring conditions (130 rpm), and mark it as slurry A.
[0060] 0.21 kg of magnesium oxide (dry basis) was dispersed in 0.6 kg of water, marked as slurry B.
[0061] 0.54kg cerium chloride solution (containing 18% CeO 2 ), 50g ferric chloride (containing 14.5g Fe 2 o 3 ) into 0.1 kg of water, marked as liquid C.
[0062] 48g ammonium metavanadate (containing 36.6g V 2 o 5 ) was added to 0.3kg of water, and 0.1kg of formic acid was added under stirring conditions (130 rpm), marked as liquid D.
[0063] Put A, B, C, and D into the colloid mill (rotating speed 2900 rpm, processing precision 2-40 microns) in sequence for 10 minutes, and then spray molding. Baked at 700°C for 2 hours, marked as S2.
[0064] The element composition, specific surface area, wear index and particle size distribution of S2 are shown in Table 1 and Table 2. CO of S2 2 adsorption infrared see ...
Embodiment 3
[0066] Add 0.589kg of pseudo-boehmite (dry basis) into 7.5kg of water, add 0.35kg of formic acid under stirring conditions (130 rpm), and mark it as slurry A.
[0067] 0.23 kg of magnesium oxide (dry basis) was dispersed in 0.6 kg of water, marked as slurry B.
[0068] 0.54kg cerium chloride solution (containing 18% CeO 2 ), 81g ferric chloride (containing 23.5g Fe 2 o 3 ) into 0.1 kg of water, marked as liquid C.
[0069] 48g ammonium metavanadate (containing 36.6g V 2 o 5 ) was added to 0.3kg of water, and 0.1kg of formic acid was added under stirring conditions (130 rpm), marked as liquid D.
[0070] Put A, B, C, and D into the colloid mill (rotating speed 2900 rpm, processing precision 2-40 microns) in sequence for 10 minutes, and then spray molding. Baked at 700°C for 2 hours, marked as S3.
[0071] The element composition, specific surface area, wear index and particle size distribution of S3 are shown in Table 1 and Table 2. CO of S3 2 adsorption infrared see ...
PUM
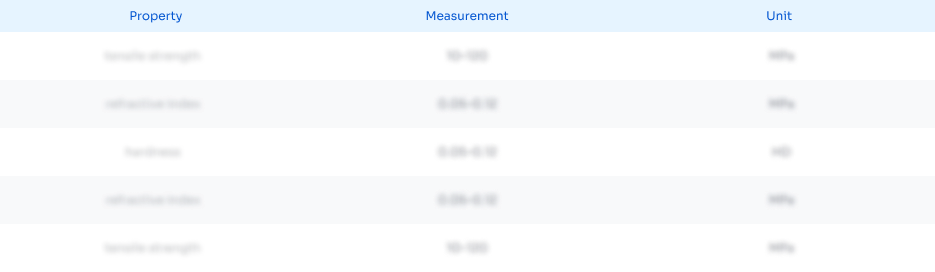
Abstract
Description
Claims
Application Information

- R&D Engineer
- R&D Manager
- IP Professional
- Industry Leading Data Capabilities
- Powerful AI technology
- Patent DNA Extraction
Browse by: Latest US Patents, China's latest patents, Technical Efficacy Thesaurus, Application Domain, Technology Topic, Popular Technical Reports.
© 2024 PatSnap. All rights reserved.Legal|Privacy policy|Modern Slavery Act Transparency Statement|Sitemap|About US| Contact US: help@patsnap.com