Polyester printing and dyeing process
A printing and dyeing technology, polyester technology, applied in the field of polyester printing and dyeing technology, can solve the problems of polyester fabric adhesion, uneven dyeing, large color difference, etc., achieve the effect of reducing color flower and improving dyeing uniformity
- Summary
- Abstract
- Description
- Claims
- Application Information
AI Technical Summary
Problems solved by technology
Method used
Image
Examples
Embodiment 1-1
[0033] 1. Compound tea saponin treatment
[0034] Add compound tea saponin to the water, add 30g of compound tea saponin per liter of water, and heat up to 100°C after the compound tea saponin dissolves; wherein the compound tea saponin is composed of bugong tea saponin and sodium silicate, silicon The consumption of sodium bicarbonate is 40wt% of bugong tea saponin, and the composition of bugong tea saponin is calculated by mass percent: nano-titanium oxide 1%, tea saponin 12%, methyl cellulose 1%, natural soap powder 23% %, 3% diatomite, 6% sepiolite, 5% sodium carbonate, and the rest is water; immerse the polyester fabric to be printed and dyed in the compound tea saponin solution at 100°C for 40 minutes, and the liquor ratio is 1:5.
[0035] Two, washing
[0036] The polyester fabric treated with compound tea saponin was washed with water.
[0037] 3. High temperature and high pressure dyeing
[0038]The polyester fabric after washing is placed in the dye solution, the ...
Embodiment 1-2
[0046] On the basis of Example 1-1, this embodiment also includes the step of recycling waste liquid, and its process flow chart is as follows figure 2 As shown, the process of waste liquid reuse is as follows:
[0047] The waste liquid produced after the compound tea saponin is processed on the polyester fabric in step 1 and the washing waste liquid in step 2 are recycled and filtered, and then enter the heat exchange system, and perform heat exchange with the normal temperature tap water entering the heat exchange system; the normal temperature tap water is passed through After the heat exchange, the temperature rises to 50°C, which is used as washing water in step 2; the temperature of the waste liquid drops to 50°C after heat exchange, and then further condenses to 8°C, and then adds dilute sulfuric acid with a concentration of 40vol% for acid analysis, acid analysis After finishing solid-liquid separation and filtering, store it as a solution used when compound tea sapon...
Embodiment 2-1
[0053] 1. Compound tea saponin treatment
[0054] Add compound tea saponin to the water, add 20g of compound tea saponin per liter of water, and heat up to 80°C after the compound tea saponin dissolves; wherein the compound tea saponin is composed of bugong tea saponin and sodium silicate, silicon The consumption of sodium bicarbonate is 25wt% of bugong tea saponin, and the composition of bugong tea saponin is calculated by mass percent: nano-titanium oxide 3%, tea saponin 18%, methyl cellulose 1%, natural soap powder 23% %, 3% diatomite, 12% sepiolite, 10% sodium carbonate, and the rest is water; immerse the polyester fabric to be printed and dyed in the compound tea saponin solution at 80°C for 20 minutes, and the liquor ratio is 1:3.
[0055] Two, washing
[0056] The polyester fabric treated with compound tea saponin was washed with water.
[0057] 3. High temperature and high pressure dyeing
[0058] The washed polyester fabric is placed in the dye solution, the dyestu...
PUM
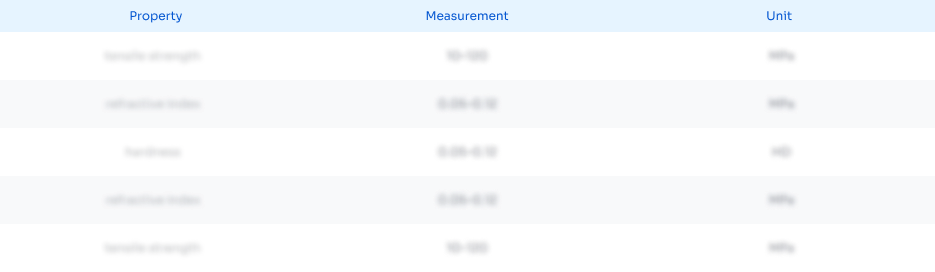
Abstract
Description
Claims
Application Information

- R&D Engineer
- R&D Manager
- IP Professional
- Industry Leading Data Capabilities
- Powerful AI technology
- Patent DNA Extraction
Browse by: Latest US Patents, China's latest patents, Technical Efficacy Thesaurus, Application Domain, Technology Topic, Popular Technical Reports.
© 2024 PatSnap. All rights reserved.Legal|Privacy policy|Modern Slavery Act Transparency Statement|Sitemap|About US| Contact US: help@patsnap.com