Phthalonitrile resin prepolymer and preparation method thereof
A kind of phthalonitrile resin, technology of phthalonitrile, applied in the field of preparation of phthalonitrile resin prepolymer
- Summary
- Abstract
- Description
- Claims
- Application Information
AI Technical Summary
Problems solved by technology
Method used
Image
Examples
Embodiment 1
[0024] Phthalonitrile resin prepolymerization:
[0025] Add biphenyl type phthalonitrile resin monomer 10g (22.83mmol), 1,7-bismethylol-m-carborane 2g (9.79mmol) to the four-necked flask, and then add 20g N-methylpyrrolidone , heated to 180° C., and mechanically stirred for 4 hours. After the reaction, the solution was poured into deionized water, stirred for 30 minutes, and filtered under reduced pressure to obtain precipitates. The precipitate was dried in an oven at 100° C. for 20 hours to obtain a biphenyl phthalonitrile resin prepolymer. The prepolymer has very good properties in ethyl acetate, acetone, tetrahydrofuran, 1,4-dioxane, N,N-dimethylformamide, N,N-dimethylacetamide and N-methylpyrrolidone. good solubility.
[0026] Prepolymer curing:
[0027] Weigh the synthesized biphenyl phthalonitrile resin prepolymer into a ceramic crucible, and solidify in a muffle furnace according to the following stepwise temperature rise program (heating rate is 5°C / min): 240°C / 2h+...
Embodiment 2
[0031] Phthalonitrile resin prepolymerization:
[0032] Add bisphenol A type phthalonitrile resin monomer 15g (31.25mmol), 1,7-bismethylol-m-carborane 1.5g (7.34mmol) to the four-necked flask, and then add 25g N,N -Dimethylformamide, heated to 150° C., mechanically stirred for 2 h, after the reaction was completed, the solution was poured into deionized water, stirred for 60 min, and filtered under reduced pressure to obtain the precipitate. The precipitate was dried in an oven at 100° C. for 20 hours to obtain a biphenyl phthalonitrile resin prepolymer. The prepolymer has very good properties in ethyl acetate, acetone, tetrahydrofuran, 1,4-dioxane, N,N-dimethylformamide, N,N-dimethylacetamide and N-methylpyrrolidone. good solubility.
[0033] Prepolymer curing:
[0034] Weigh the synthesized bisphenol A phthalonitrile resin prepolymer into a ceramic crucible, and cure it in a muffle furnace according to the following stepwise temperature rise program (heating rate is 5°C / m...
Embodiment 3
[0037] Phthalonitrile resin prepolymerization:
[0038] Add biphenyl type phthalonitrile resin monomer 30g (68.49mmol), 1,7-bismethylol-m-carborane 8g (39.16mmol) into the four-necked flask, then add 40g N,N-di Methylacetamide was heated to 165° C. and mechanically stirred for 6 hours. After the reaction, the solution was poured into deionized water, stirred for 10 minutes, and filtered under reduced pressure to obtain precipitates. The precipitate was dried in an oven at 100° C. for 5 hours to obtain a biphenyl phthalonitrile resin prepolymer. The prepolymer has very good properties in ethyl acetate, acetone, tetrahydrofuran, 1,4-dioxane, N,N-dimethylformamide, N,N-dimethylacetamide and N-methylpyrrolidone. good solubility.
[0039] Prepolymer curing:
[0040] Weigh the synthesized biphenyl phthalonitrile resin prepolymer into a ceramic crucible, and solidify in a muffle furnace according to the following stepwise temperature rise program (heating rate is 5°C / min): 240°C / 2h+...
PUM
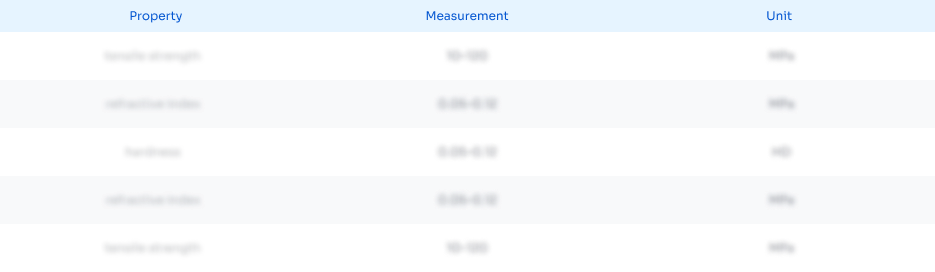
Abstract
Description
Claims
Application Information

- R&D Engineer
- R&D Manager
- IP Professional
- Industry Leading Data Capabilities
- Powerful AI technology
- Patent DNA Extraction
Browse by: Latest US Patents, China's latest patents, Technical Efficacy Thesaurus, Application Domain, Technology Topic, Popular Technical Reports.
© 2024 PatSnap. All rights reserved.Legal|Privacy policy|Modern Slavery Act Transparency Statement|Sitemap|About US| Contact US: help@patsnap.com