Method for completely depolymerizing polytetrahydrofuran in anhydrous environment
A polytetrahydrofuran, water-free environment technology, applied in the direction of organic chemistry, can solve the problems of reducing production costs, increasing the risk of polluting the environment, and not being able to achieve full-load depolymerization, so as to achieve the effect of controlling production costs
- Summary
- Abstract
- Description
- Claims
- Application Information
AI Technical Summary
Problems solved by technology
Method used
Image
Examples
Embodiment 1
[0022] Embodiment 1: as attached figure 1 Shown, the method that this polytetrahydrofuran is all depolymerized under anhydrous environment, carries out as follows:
[0023] Add 98% concentrated sulfuric acid into the depolymerization reactor 2, preheat the polytetrahydrofuran (PTMEG) to 145°C to 160°C through the feed preheater 1, and add the preheated polytetrahydrofuran into the depolymerization reactor 2 , under the catalysis of 98% concentrated sulfuric acid, polytetrahydrofuran undergoes depolymerization reaction in depolymerization reactor 2 at a temperature of 95°C to 105°C, and the gas phase containing tetrahydrofuran generated by depolymerization enters the reaction through the top of reactor tower 3 The tower top condenser 4 is cooled, and the tetrahydrofuran liquid phase that cooling obtains obtains tetrahydrofuran after being neutralized by alkaline solution; Wherein, when adding 98% vitriol oil to depolymerization reactor 2, the add-on of 98% vitriol oil does not ...
Embodiment 2
[0028] Embodiment 2: As an optimization of the above embodiment, before adding 98% concentrated sulfuric acid to the depolymerization reactor 2, it is necessary to reduce the tar concentration in the depolymerization reactor 2 to below 5%.
Embodiment 3
[0029] Example 3: The liquid-phase tetrahydrofuran obtained by condensing the condenser 4 at the top of the reactor is the product, and the gas phase components that cannot be condensed are condensed and recovered by the vent condenser 6 again and then sent to vent.
PUM
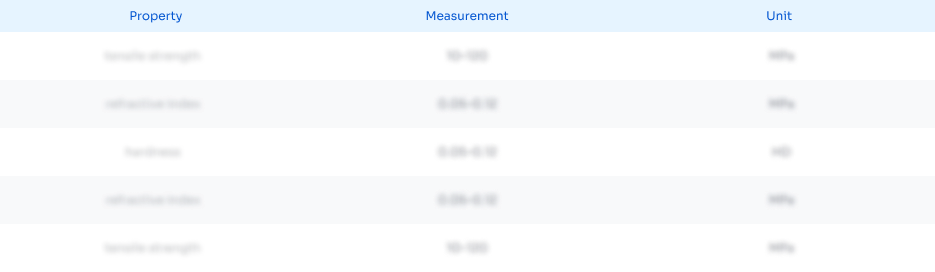
Abstract
Description
Claims
Application Information

- R&D Engineer
- R&D Manager
- IP Professional
- Industry Leading Data Capabilities
- Powerful AI technology
- Patent DNA Extraction
Browse by: Latest US Patents, China's latest patents, Technical Efficacy Thesaurus, Application Domain, Technology Topic, Popular Technical Reports.
© 2024 PatSnap. All rights reserved.Legal|Privacy policy|Modern Slavery Act Transparency Statement|Sitemap|About US| Contact US: help@patsnap.com