Composite ionic liquid catalyst, and preparation method and application thereof
A technology of liquid catalyst and compound ion, which is applied in the field of alkylation reaction and compound ionic liquid catalyst, can solve the problems of complex operating conditions, undisclosed ethylene conversion rate, poor selectivity, etc., and achieve reduced cracking reactions, good catalytic effect, and increased selective effect
- Summary
- Abstract
- Description
- Claims
- Application Information
AI Technical Summary
Problems solved by technology
Method used
Image
Examples
Embodiment 1
[0034]Accurately weigh 10.32 g (0.075 mol) of triethylamine hydrochloride and add it to a 100 ml three-necked flask replaced with nitrogen, and nitrogen gas is fed continuously during the reaction. Accurately weigh 20g (0.15mol) of anhydrous aluminum chloride and slowly add it to the flask in 4 times, start stirring, stir at room temperature for 30min, raise the temperature of the water bath to 50°C, continue to stir and react for 6 hours, and obtain after complete reaction Homogeneous liquid A, then add 3.63g (0.015mol) ferric nitrate to the above-mentioned liquid A system, raise the temperature of the water bath to 100°C and continue the reaction for 6 hours until the ferric nitrate is completely reacted to obtain a composite ionic liquid catalyst system.
Embodiment 2
[0036] Accurately weigh 13.10 g (0.075 mol) of 1-butyl-3-methylimidazolium chloride salt and add it to a 100 ml three-necked flask replaced with nitrogen, and nitrogen gas is continuously fed during the reaction. Accurately weigh 20g (0.15mol) of anhydrous aluminum chloride into the flask slowly in 3 times, start stirring, stir at room temperature for 30min, raise the temperature of the water bath to 80°C, continue stirring for 6 hours, and obtain after complete reaction Homogeneous liquid A, then add 3.63g (0.015mol) ferric nitrate to the above-mentioned liquid A system, raise the temperature of the water bath to 100°C and continue the reaction for 6 hours until the ferric nitrate is completely reacted to obtain a composite ionic liquid catalyst system.
Embodiment 3
[0038] Accurately weigh 7.17 g (0.075 mol) of trimethylamine hydrochloride and add it into a 100 ml three-necked flask replaced with nitrogen, and nitrogen gas is continuously fed in during the reaction. Accurately weigh 20g (0.15mol) of anhydrous aluminum chloride and slowly add it to the flask in 4 times, start stirring, stir at room temperature for 30min, raise the temperature of the water bath to 50°C, continue to stir and react for 6 hours, and obtain after complete reaction Homogeneous liquid A, then add 3.63g (0.015mol) ferric nitrate to the above-mentioned liquid A system, raise the temperature of the water bath to 100°C and continue the reaction for 6 hours until the ferric nitrate is completely reacted to obtain a composite ionic liquid catalyst system.
PUM
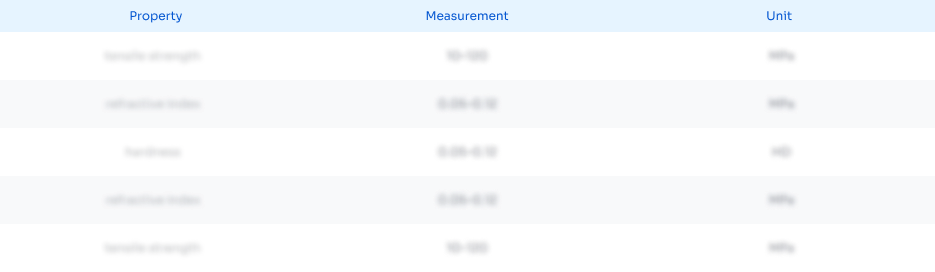
Abstract
Description
Claims
Application Information

- Generate Ideas
- Intellectual Property
- Life Sciences
- Materials
- Tech Scout
- Unparalleled Data Quality
- Higher Quality Content
- 60% Fewer Hallucinations
Browse by: Latest US Patents, China's latest patents, Technical Efficacy Thesaurus, Application Domain, Technology Topic, Popular Technical Reports.
© 2025 PatSnap. All rights reserved.Legal|Privacy policy|Modern Slavery Act Transparency Statement|Sitemap|About US| Contact US: help@patsnap.com