MEMS inertial sensor low-stress packaging structure and method based on graphical gold-tin soldering
An inertial sensor and packaging method technology, applied in the field of micro-electromechanical, can solve problems affecting device reliability, reduce packaging stress, reduce vibration and shock resistance, etc., to reduce effective contact area, reduce packaging stress, and structural rigidity big effect
- Summary
- Abstract
- Description
- Claims
- Application Information
AI Technical Summary
Problems solved by technology
Method used
Image
Examples
Embodiment Construction
[0015] The present invention will be further introduced below in conjunction with the accompanying drawings and specific embodiments.
[0016] The present invention is based on the MEMS inertial sensor low-stress packaging structure of patterned gold-tin soldering, including MEMS inertial sensor chip 1, adhesive glue 2, transition layer 3, gold-tin soldering layer 4, packaging tube shell 5, lead wire 6 and cover plate 7 .
[0017] to combine figure 1 The material of the package shell 5 is ceramic or metal, the shape is rectangular or circular, and the bottom of the cavity of the package shell 5 is plated with a layer of gold.
[0018] The material of the transition layer 3 is the same as the substrate material of the MEMS inertial sensor chip, which is silicon or glass. A patterned gold layer 3a is plated on the bottom of the transition layer 3 using a MEMS process.
[0019] The transition layer 3 is welded on the package shell 5 by gold-tin soldering process, and a pattern...
PUM
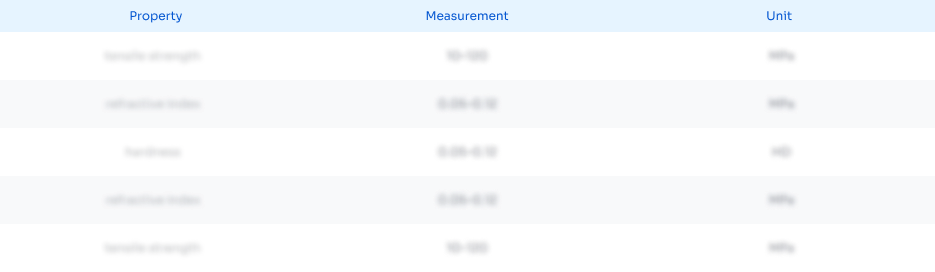
Abstract
Description
Claims
Application Information

- Generate Ideas
- Intellectual Property
- Life Sciences
- Materials
- Tech Scout
- Unparalleled Data Quality
- Higher Quality Content
- 60% Fewer Hallucinations
Browse by: Latest US Patents, China's latest patents, Technical Efficacy Thesaurus, Application Domain, Technology Topic, Popular Technical Reports.
© 2025 PatSnap. All rights reserved.Legal|Privacy policy|Modern Slavery Act Transparency Statement|Sitemap|About US| Contact US: help@patsnap.com