Method for removing organochlorine in waste lubricating oil
A technology for waste lubricating oil and organic chlorine, which is applied in the directions of lubricating composition and multi-stage series refining process treatment, can solve the problem of low removal rate of organic chlorine, reduce the corrosion of hydrogenation equipment, widen sources, reduce The effect of organochlorine content
- Summary
- Abstract
- Description
- Claims
- Application Information
AI Technical Summary
Problems solved by technology
Method used
Image
Examples
Embodiment 1
[0022] Example 1. Polyethylene glycol monomethyl ether (MPEG-750) and potassium hydroxide were stirred to a homogeneous phase at 90°C and then reacted for 1 hour to obtain dechlorination agent 1#. Heat the waste lubricating oil containing 950ppm organic chlorine to 130°C after dehydration and removal of impurities, add dechlorination agent 1# and accelerator to the waste lubricating oil, stir the material for 2.5 hours, take oil samples for total Chlorine analysis.
[0023] According to the detection and analysis of this embodiment, it is found that the removal rate of organic chlorine reaches 95% when the accelerator aluminum is added to the reaction system; the organic chlorine removal rate reaches 93% when the accelerator nickel is added to the reaction system.
Embodiment 2
[0024] Example 2. Polyethylene glycol monomethyl ether (MPEG-400) and sodium carbonate were stirred at 110°C to a homogeneous phase and then reacted for 1 hour to obtain dechlorination agent 2#. Heat the waste lubricating oil containing 870ppm organic chlorine to 110°C after dehydrating and removing impurities, add dechlorinating agent 2# and accelerator to the waste lubricating oil, stir the material for 1.5 hours, and take oil samples for total Chlorine analysis.
[0025] According to the detection and analysis of this embodiment, it is found that the removal rate of organic chlorine reaches 92% when the accelerator aluminum is added to the reaction system; the organic chlorine removal rate reaches 93.8% when the accelerator nickel is added to the reaction system.
Embodiment 3
[0026] Example 3. Polyethylene glycol (PEG-200) and potassium carbonate were stirred to a homogeneous phase at 120°C and then reacted for 2 hours to obtain dechlorination agent 3#. Heat the waste lubricating oil containing 1260ppm organic chlorine to 80°C after dehydration and removal of impurities, add dechlorination agent 3# and accelerator aluminum to the waste lubricating oil, stir the material for 4 hours, take oil samples for total Chlorine analysis.
[0027] According to the detection and analysis of this example, it was found that after the reaction system was stirred for 4 hours, the removal rate of organic chlorine reached 93%, and when the dechlorination time was extended to 8 hours, the removal rate of organic chlorine reached 95.7%.
PUM
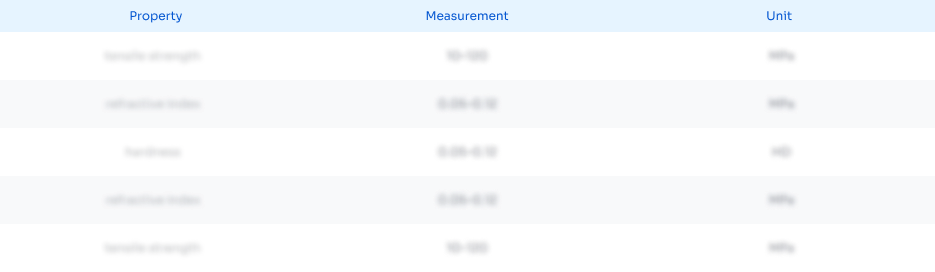
Abstract
Description
Claims
Application Information

- R&D
- Intellectual Property
- Life Sciences
- Materials
- Tech Scout
- Unparalleled Data Quality
- Higher Quality Content
- 60% Fewer Hallucinations
Browse by: Latest US Patents, China's latest patents, Technical Efficacy Thesaurus, Application Domain, Technology Topic, Popular Technical Reports.
© 2025 PatSnap. All rights reserved.Legal|Privacy policy|Modern Slavery Act Transparency Statement|Sitemap|About US| Contact US: help@patsnap.com