A low-cost aluminum-based photovoltaic ribbon and its preparation method
A technology for photovoltaic ribbons and aluminum substrates, applied in the direction of metal material coating process, coating, fusion spraying, etc., can solve the problems of insufficient connectivity, affect the efficiency of photovoltaic ribbons, increase production costs, etc., and achieve simple structure , Uniform coating, improve the effect of heat dissipation
- Summary
- Abstract
- Description
- Claims
- Application Information
AI Technical Summary
Problems solved by technology
Method used
Image
Examples
Embodiment 1
[0050] see Figure 1-4 As shown, a low-cost aluminum-based photovoltaic ribbon, including an aluminum core 2, an outer copper strip 23, and a tin layer 24;
[0051] The outer wall of the aluminum core 2 is covered with an outsourcing copper strip 23 through the coating device, and the outer wall of the outsourcing copper strip 23 is sprayed with a tin layer 24 through the spraying and drying device 9;
[0052] The coating device, the limiting device 8 and the spraying and drying device 9 are arranged side by side, and the coating device, the limiting device 8 and the spraying and drying device 9 are all installed on the top surface of the base 1 through the support rod 3 .
[0053] The cladding device includes a bearing seat 4, a hollow tube 5, a connecting rod 6, a winding wheel 7 and a driving mechanism; the outer wall of the hollow tube 5 is provided with a bearing seat 4, and the bearing seat 4 is installed on the support rod 3, and the middle One end of the empty pipe 5 ...
Embodiment 2
[0071] Compared with embodiment 1, the difference is:
[0072] Step 1: Add the aluminum material into the melting furnace, and add graphene at 800°C for mixing, and then cool to room temperature to obtain the aluminum core 2;
[0073] The preparation process of graphene comprises the following steps:
[0074] S1. Add graphite powder, potassium persulfate and phosphorus pentoxide to concentrated sulfuric acid, and stir for 4 hours at a temperature of 80°C; obtain mixture A; control the quality of graphite powder, potassium persulfate, phosphorus pentoxide and concentrated sulfuric acid The ratio is 5:5:5:13;
[0075] S2. Cool mixture A to room temperature, mix with deionized water and stir at 0°C for 10 hours to obtain mixture B; then filter mixture B, wash with deionized water, and dry to obtain solid C; control A The mass ratio of mixture and deionized water is 30:1000;
[0076] S3. Disperse the C solid in concentrated sulfuric acid, then add potassium permanganate five ti...
PUM
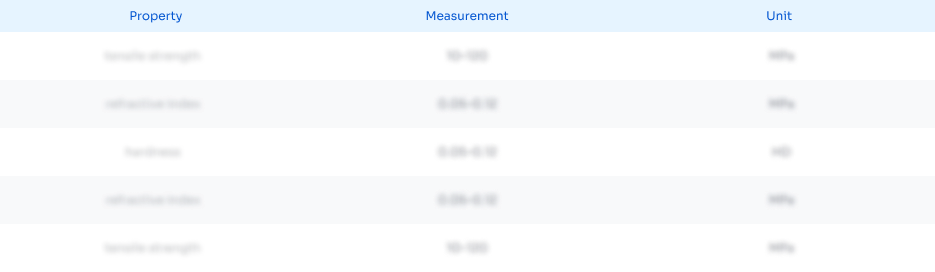
Abstract
Description
Claims
Application Information

- R&D Engineer
- R&D Manager
- IP Professional
- Industry Leading Data Capabilities
- Powerful AI technology
- Patent DNA Extraction
Browse by: Latest US Patents, China's latest patents, Technical Efficacy Thesaurus, Application Domain, Technology Topic, Popular Technical Reports.
© 2024 PatSnap. All rights reserved.Legal|Privacy policy|Modern Slavery Act Transparency Statement|Sitemap|About US| Contact US: help@patsnap.com