Preparation method of furoic acid
A technology for furoic acid and furfural, applied in the field of preparation of furoic acid, can solve problems such as complex acid treatment, and achieve the effects of simplified post-processing steps, low cost, and good industrial application prospects
- Summary
- Abstract
- Description
- Claims
- Application Information
AI Technical Summary
Problems solved by technology
Method used
Examples
preparation example Construction
[0021] The invention provides a method for preparing furoic acid, comprising: contacting an aqueous solution of furfural with a catalyst under air and / or oxygen conditions, and performing a catalytic oxidation reaction to obtain furoic acid, wherein the catalyst is obtained by the following steps: a carrier, an alkali The neutral nitrogen-containing compound and the precursor of the active component are mixed and placed in a solvent, heated in a water bath and subjected to reflux and stirring treatment; the mixture after the reflux and stirring treatment is sequentially subjected to drying treatment and roasting reduction treatment to obtain a catalyst; wherein, the active component The precursor is selected from rhodium chloride (RhCl 3 ), palladium chloride (PdCl 2 ), chloroplatinic acid (H 2 PtCl 6 ) and ruthenium chloride (RuCl 3 ), the carrier is selected from activated carbon (AC), graphite (C), fullerene (C 60 ) and graphene oxide (GO) in one or more.
[0022] For ...
preparation example 1
[0037] The preparation of preparation example 1 catalyst Rh / AC
[0038] Mix 2g of carrier activated carbon AC, 6g of bipyridine with 120g of 25wt% ethanol and 75wt% water, add RhCl 3 , wherein the mass ratio of metal Rh to carrier activated carbon AC is 0.05:1, reflux and stir treatment in a 70°C water bath for 8h, separate the treated solid, and then dry it in an oven at 120°C for 16h, and then calculate the volume percentage in 20%H 2 and 80%N 2 The atmosphere was reduced and calcined at 650° C. for 4 hours to obtain a catalyst Rh / AC with an active component content (ie, metal element content) of 4.7 wt%.
preparation example 2
[0039] The preparation of preparation example 2 catalyst Rh / AC
[0040] Mix 2g of carrier activated carbon AC, 10g of melamine with 130g of 20wt% ethanol and 70wt% water, add RhCl 3 , wherein the mass ratio of the metal Rh to the carrier activated carbon AC is 0.06:1, reflux and stir treatment in a 60°C water bath for 10h, separate the treated solid, and then dry it in an oven at 110°C for 18h, and then by volume percentage, in 30%H 2 and 70%N 2 The atmosphere was reduced and calcined at 750° C. for 3 hours to obtain a catalyst Rh / AC with an active component content of 5.6 wt%.
PUM
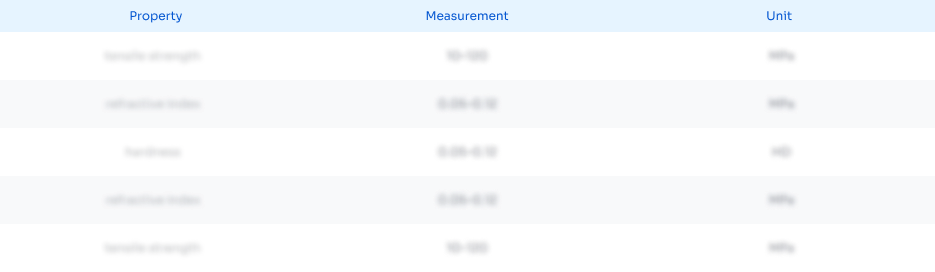
Abstract
Description
Claims
Application Information

- Generate Ideas
- Intellectual Property
- Life Sciences
- Materials
- Tech Scout
- Unparalleled Data Quality
- Higher Quality Content
- 60% Fewer Hallucinations
Browse by: Latest US Patents, China's latest patents, Technical Efficacy Thesaurus, Application Domain, Technology Topic, Popular Technical Reports.
© 2025 PatSnap. All rights reserved.Legal|Privacy policy|Modern Slavery Act Transparency Statement|Sitemap|About US| Contact US: help@patsnap.com