Bisphenol A SMC mold pressing resin composition and preparation method thereof
A resin composition and molding technology, which is applied in the field of SMC molding, can solve the problems of supply, resin manufacturers have no models, and cannot make strong acid and alkali resistant and high temperature molded products, etc.
- Summary
- Abstract
- Description
- Claims
- Application Information
AI Technical Summary
Problems solved by technology
Method used
Image
Examples
Embodiment 1
[0024] According to parts by weight, weigh the raw material components, including 20.7 parts of bisphenol A type 3301 resin, 6.6 parts of low shrinkage unsaturated polyester resin, 0.34 parts of tert-butyl perbenzoate, 0.94 parts of zinc stearate, 0.018 parts of oil ester Parts, 34.22 parts of filler (calcium carbonate powder particle size is 600 mesh), 36.96 parts of fiber (2400 non-alkali roving), 0.22 part of magnesium oxide, 0.002 part of cobalt naphthenate;
[0025] Add bisphenol A type 3301 resin, low-shrinkage unsaturated polyester resin, and tert-butyl perbenzoate in sequence in the stirrer, and stir at a stirring speed of 500r / min for 2 minutes;
[0026] Add oil and stir for 3 minutes;
[0027] Add zinc stearate, stirring time is 2 minutes;
[0028] Add 10% of the filler, stir for 1 minute, add cobalt naphthenate and stir, increase the stirring speed to 600r / min, and stir for 1 minute;
[0029] Add color paste and stir for 2 minutes;
[0030] Add the remaining fill...
Embodiment 2
[0034] Different from Example 1, 18.6 parts of bisphenol A type 3301 resin, 5.3 parts of low shrinkage unsaturated polyester resin, 0.48 parts of tert-butyl perbenzoate, 1.5 parts of zinc stearate, 0.009 parts of oil ester, 26.5 parts of filler parts (aluminum hydroxide particle size is 400 mesh), 27.8 parts of fibers, 0.15 parts of magnesium oxide, 0.0026 parts of cobalt naphthenate;
Embodiment 3
[0036] Different from Example 1, 22.7 parts of bisphenol A type 3301 resin, 7.3 parts of low shrinkage unsaturated polyester resin, 0.2 parts of tert-butyl perbenzoate, 0.6 parts of zinc stearate, 0.022 parts of oil ester, 37.9 parts of filler parts (calcium carbonate powder particle size is 800 mesh), fiber 46.5 parts, magnesium oxide 0.27 parts, cobalt naphthenate 0.0014 parts;
PUM
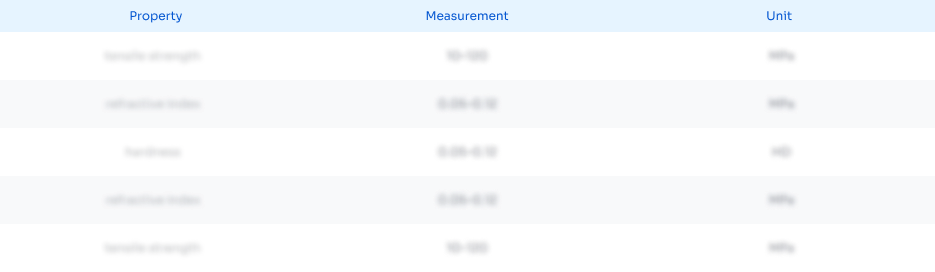
Abstract
Description
Claims
Application Information

- R&D
- Intellectual Property
- Life Sciences
- Materials
- Tech Scout
- Unparalleled Data Quality
- Higher Quality Content
- 60% Fewer Hallucinations
Browse by: Latest US Patents, China's latest patents, Technical Efficacy Thesaurus, Application Domain, Technology Topic, Popular Technical Reports.
© 2025 PatSnap. All rights reserved.Legal|Privacy policy|Modern Slavery Act Transparency Statement|Sitemap|About US| Contact US: help@patsnap.com