Mixed slow-release snow-melting deicing material as well as preparation method and application method thereof
An application method and snow melting technology, applied in the direction of chemical instruments and methods, other chemical processes, etc., can solve problems such as increasing environmental pressure, increasing manufacturing difficulty, and pressure limitation due to metal erosion
- Summary
- Abstract
- Description
- Claims
- Application Information
AI Technical Summary
Problems solved by technology
Method used
Examples
Embodiment 1
[0044] Put 250.38g of NaCl into a pulverizer, pass through a 20-mesh sieve after crushing, add 25.36g of carboxymethyl cellulose, and mix evenly in a high-speed mechanical agitator to obtain a snow-melting salt mixture, which is sealed and packaged for use.
[0045] CaSO 4 2H 2 O 321.13g of gypsum powder with a mass content of not less than 80% was put into a pulverizer and crushed, passed through a 20-mesh sieve, and CaHPO was added 4 2.63 g was uniformly mixed in high-speed mechanical stirring to obtain a gelling material mixture, which was sealed and packaged for use.
[0046] Take 0.5g of each of the two mixed materials, mix them evenly, and after keeping the temperature at -15°C for 3 hours, apply them directly on an ice cube of 5cm×3cm×1cm weighing about 15g.
[0047] As a comparison, 1g of NaCl was also placed on ice cubes of the same environment and the same specifications, and the rest were tested in accordance with the relevant provisions of the national standard ...
Embodiment 2
[0049] Put 250.38g of NaCl into a pulverizer, pass through a 20-mesh sieve after crushing, add 25.36g of carboxymethylcellulose, and mix evenly in a high-speed mechanical agitator to obtain a mixture of snow-melting salt, which is sealed and packaged for use.
[0050] CaSO 4 2H 2 O 321.13g of gypsum powder with a mass content of not less than 80% was put into a pulverizer and crushed, passed through a 20-mesh sieve, and CaHPO was added 4 2.63 g was uniformly mixed in high-speed mechanical stirring to obtain a gelling material mixture, which was sealed and packaged for use.
[0051] Take 0.5g of the two mixed materials and mix them with 0.5g of granite chips evenly. After keeping the temperature at -15°C for 3 hours, apply them on an ice cube of 5cm×3cm×1cm weighing about 15g.
[0052] As a comparison, 1g of NaCl was also placed on ice cubes of the same environment and the same specifications, and the rest were tested in accordance with the relevant provisions of the nationa...
Embodiment 3
[0054] NaCl 301.52g and CaCl 2 2H 2 O 50.93g were put into the pulverizer together, crushed and passed through a 20-mesh sieve, 31.96g of carboxymethylcellulose was added, and mixed evenly in high-speed mechanical stirring to obtain a mixture of snow-melting salt, which was sealed and packaged for use.
[0055] CaSO 4 2H 2 O 559.35g of gypsum powder with a mass content of not less than 80% and slaked lime powder with a mass content of not less than 85% of CaO 59.06g, put them together in a pulverizer and crush them, pass through a 20-mesh sieve, and add KH 2 PO 4 37.63 g was uniformly mixed in high-speed mechanical stirring to obtain a gelling material mixture, which was sealed and packaged for use.
[0056] Take 0.5g of the two mixed materials and mix them with 0.5g of granite chips evenly. After keeping the temperature at -15°C for 3 hours, apply them on an ice cube of 5cm×3cm×1cm weighing about 15g.
[0057] As a comparison, 1g of NaCl was also placed on ice cubes of t...
PUM
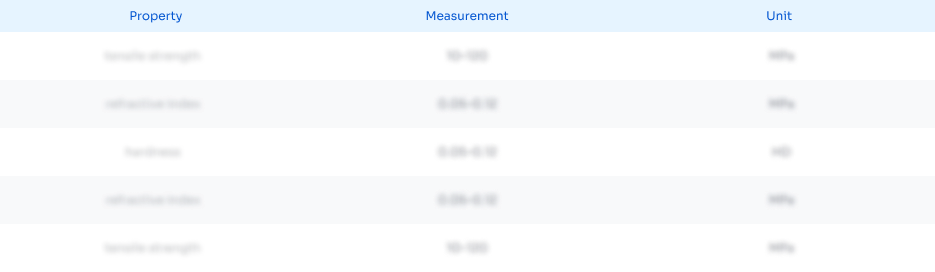
Abstract
Description
Claims
Application Information

- Generate Ideas
- Intellectual Property
- Life Sciences
- Materials
- Tech Scout
- Unparalleled Data Quality
- Higher Quality Content
- 60% Fewer Hallucinations
Browse by: Latest US Patents, China's latest patents, Technical Efficacy Thesaurus, Application Domain, Technology Topic, Popular Technical Reports.
© 2025 PatSnap. All rights reserved.Legal|Privacy policy|Modern Slavery Act Transparency Statement|Sitemap|About US| Contact US: help@patsnap.com