Die head hot air temperature control method and control system applied to melt-blown fabric production
A temperature control method, hot air technology, applied in the direction of feeding the solution to the spinneret, melt spinning, non-woven fabrics, etc., can solve the problems of difficult loss of residual heat of the air heater, poor continuity, and uneven cloth quality. Achieve the effects of improving stability and product quality, avoiding damage caused by high heat, and expanding the range of materials
- Summary
- Abstract
- Description
- Claims
- Application Information
AI Technical Summary
Problems solved by technology
Method used
Image
Examples
Embodiment Construction
[0024] Embodiments of the present invention are described in detail below, examples of which are shown in the drawings, wherein the same or similar reference numerals designate the same or similar elements or elements having the same or similar functions throughout. The embodiments described below by referring to the figures are exemplary only for explaining the present invention and should not be construed as limiting the present invention.
[0025] In the description of the present invention, reference to the terms "one embodiment," "some embodiments," "exemplary embodiments," "examples," "specific examples," or "some examples" is intended to mean that the embodiments are A specific feature, structure, material, or characteristic described by or example is included in at least one embodiment or example of the present invention. In this specification, schematic representations of the above terms do not necessarily refer to the same embodiment or example. Furthermore, the spe...
PUM
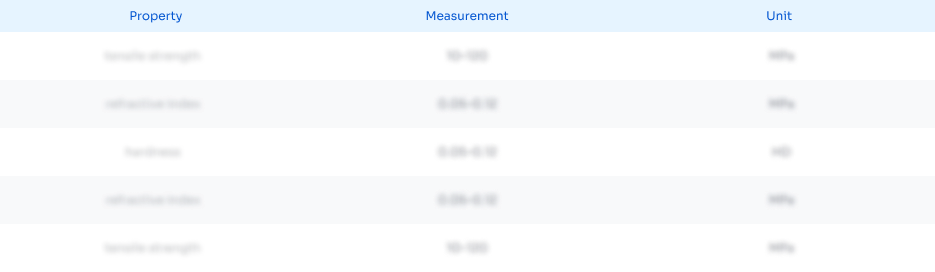
Abstract
Description
Claims
Application Information

- R&D
- Intellectual Property
- Life Sciences
- Materials
- Tech Scout
- Unparalleled Data Quality
- Higher Quality Content
- 60% Fewer Hallucinations
Browse by: Latest US Patents, China's latest patents, Technical Efficacy Thesaurus, Application Domain, Technology Topic, Popular Technical Reports.
© 2025 PatSnap. All rights reserved.Legal|Privacy policy|Modern Slavery Act Transparency Statement|Sitemap|About US| Contact US: help@patsnap.com