Method for producing active magnesium oxide from spice waste residues
A technology of active magnesium oxide and magnesium hydroxide, applied in magnesium oxide, magnesium carbonate and other directions, can solve the problems of large water and thermal energy consumption, high energy consumption, low solubility, etc., achieve significant economic and ecological benefits, and promote the effective use of resources. The effect of utilization and ecological environment protection
- Summary
- Abstract
- Description
- Claims
- Application Information
AI Technical Summary
Problems solved by technology
Method used
Examples
Embodiment 1
[0027] Take the basic magnesium chloride waste residue produced in the production of ethyl maltol and put it into the reaction kettle, add clean water 2.3 times its mass, stir and beat, heat to 100°C and distill for 2 hours; press filter to obtain magnesium hydroxide filter cake and magnesium chloride mother liquor , add 4% by volume of 27.5% hydrogen peroxide to the magnesium oxide mother liquor, control the temperature at 85°C, stir for 10 minutes, digest the organic impurities in the mother liquor, separate by pressure filtration, and obtain the colorless magnesium chloride mother liquor; analyze the magnesium chloride in the colorless magnesium chloride mother liquor content, measure its volume and density, calculate its mass of magnesium chloride, add 75% of its mass of ammonium bicarbonate and 35% of 20% ammonia water, maintain the temperature at 65°C for 70 minutes under stirring, and generate basic magnesium carbonate Suspension: press filter to separate the suspension ...
Embodiment 2
[0029] Take the basic magnesium chloride waste slag produced in the production of maltol and put it into the reaction kettle, add clean water 2.6 times its mass, stir and beat, heat to 103°C and distill for 2.2 hours; press filter to obtain magnesium hydroxide filter cake and magnesium chloride mother liquor, and pour Add 27.5% hydrogen peroxide of 5% by volume to the magnesium oxide mother liquor, control the temperature at 90°C, stir for 12 minutes, digest the organic impurities in the mother liquor, separate by pressure filtration, and obtain the colorless magnesium chloride mother liquor; analyze the magnesium chloride content of the colorless magnesium chloride mother liquor, Measure its volume and density, calculate its mass of magnesium chloride, add 80% of its mass ammonium bicarbonate and 40% of 20% ammonia water, maintain the temperature at 70°C for 75 minutes while stirring, and generate basic magnesium carbonate suspension liquid; press filtration to separate the su...
Embodiment 3
[0031] Take the basic magnesium chloride waste residue produced in the production of spices and put it into the reaction kettle, add clean water 2.8 times its mass, stir and beat, heat to 105°C and distill for 2.5 hours; press filter to obtain magnesium hydroxide filter cake and magnesium chloride mother liquor, and pour into the magnesium oxide Add 6% by volume of 27.5% hydrogen peroxide to the mother liquor, control the temperature at 90°C, stir for 15 minutes, digest the organic impurities in the mother liquor, separate by pressure filtration, and obtain the colorless magnesium chloride mother liquor; analyze the magnesium chloride content of the colorless magnesium chloride mother liquor, and measure its Volume and density, calculate its magnesium chloride quality, add its mass 85% of ammonium bicarbonate and 35% of 20% ammonia water, keep the temperature at 70°C for 70 minutes while stirring, and generate basic magnesium carbonate suspension; The suspension was separated b...
PUM
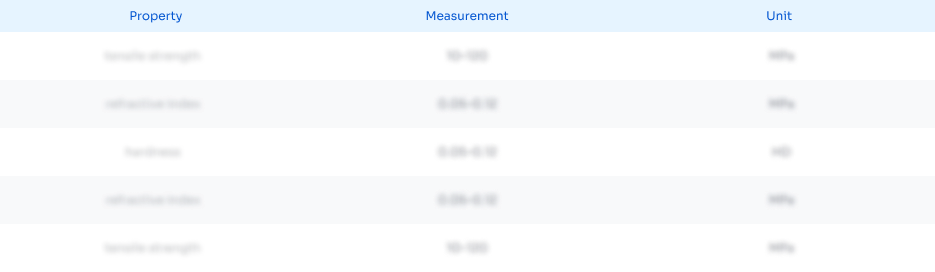
Abstract
Description
Claims
Application Information

- R&D
- Intellectual Property
- Life Sciences
- Materials
- Tech Scout
- Unparalleled Data Quality
- Higher Quality Content
- 60% Fewer Hallucinations
Browse by: Latest US Patents, China's latest patents, Technical Efficacy Thesaurus, Application Domain, Technology Topic, Popular Technical Reports.
© 2025 PatSnap. All rights reserved.Legal|Privacy policy|Modern Slavery Act Transparency Statement|Sitemap|About US| Contact US: help@patsnap.com