Handling method for using aluminum sulfate slag as cement ingredient
A technology of aluminum sulfate slag and treatment method, applied in the direction of cement production and the like, can solve the problems of reducing cement hydration capacity, reducing cost, and reducing production efficiency, so as to overcome energy consumption, reduce production efficiency, and improve cement Gel properties, the effect of reducing the cost of cement
- Summary
- Abstract
- Description
- Claims
- Application Information
AI Technical Summary
Problems solved by technology
Method used
Examples
Embodiment 1
[0013] The parts by weight are: 2 parts of aluminum sulfate slag, 1.5 parts of acetylene gas slag, 1.5 parts of fly ash and an appropriate amount of water to make a 6 × 12 × 24 cm block, and then dry it naturally to form a green block; Put it in a kiln for roasting, when the roasting temperature reaches 620°C, cool it out of the kiln, and grind it into powder into aluminum sulfate slag product. The aluminum sulfate slag product is mixed in a certain proportion and used to replace the commercial slag cement as the cementitious material and the commercial slag cement as the cementitious material, and the physical properties such as strength and wear resistance are tested according to the relevant ISO cement physical property test standards, (ie The ratio of mortar to sand is 1:3, the ratio of water to cement is 0.5, 450 grams of cementitious material can be used, 1350 grams of standard sand, the size of the test block is 4×4×16cm, and each composition is 3 pieces, demoulding, cur...
Embodiment 2
[0017] The parts by weight are: 3 parts of aluminum sulfate slag, 1 part of acetylene gas slag, 1 part of fly ash and an appropriate amount of water to make a 8 × 16 × 30cm block, and then dry it naturally to form a green block; Put it in a kiln for roasting, when the roasting temperature reaches 320°C, cool it out of the kiln, take the processed aluminum sulfate slag as 1 part and cement clinker plus gypsum as 1 part, mix and grind it into powder according to the weight ratio, referred to as mixed powder, Then mix it with commercial slag powder to form a cementitious material, and compare the performance with commercial ordinary cement and road cement according to the ISO relevant cement physical performance test standards. The results are shown in Table 2.
[0018] Preface
[0019] It can be seen from Table 2 that the anti-wear performance, flexural strength and compressive strength of the existing commercial slag powder mixed with a certain proportion of aluminum s...
Embodiment 3
[0021] The parts by weight are: 1.5 parts of aluminum sulfate slag, 1.5 parts of acetylene gas slag, 2 parts of fly ash and an appropriate amount of water to make a 10 × 16 × 30cm compact, and then dry it naturally to form a green compact; Put it in a kiln for roasting, when the roasting temperature is 450°C, cool it out of the kiln, and grind it into powder to be aluminum sulfate slag product. The aluminum sulfate slag product is mixed in a certain proportion and used to replace the pure clinker cement as the cementitious material and the pure clinker cement as the cementitious material. The physical properties such as strength and wear resistance are tested and compared according to the ISO relevant cement physical property test standards. The result example is in Table 3.
[0022]
Preface
Sample weight (g)
Loss after abrasion
Weight (g)
Flexural strength (mpa)
Compressive strength (mpa)
No
...
PUM
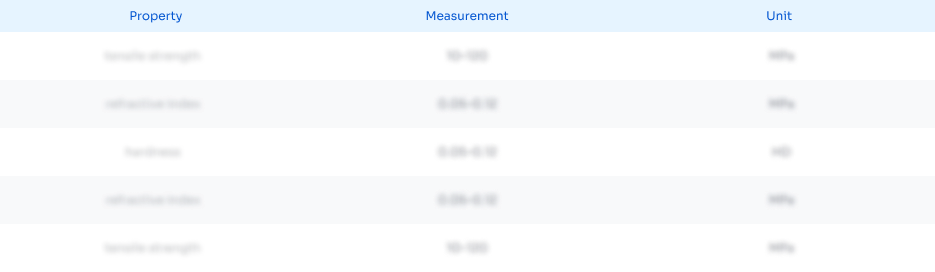
Abstract
Description
Claims
Application Information

- R&D
- Intellectual Property
- Life Sciences
- Materials
- Tech Scout
- Unparalleled Data Quality
- Higher Quality Content
- 60% Fewer Hallucinations
Browse by: Latest US Patents, China's latest patents, Technical Efficacy Thesaurus, Application Domain, Technology Topic, Popular Technical Reports.
© 2025 PatSnap. All rights reserved.Legal|Privacy policy|Modern Slavery Act Transparency Statement|Sitemap|About US| Contact US: help@patsnap.com