Leather finishing agent and production method thereof
A technology of leather finishing agent and acrylonitrile, which is applied in the field of finishing agents, can solve the problems of high cost and failure to meet the requirements of undercoated leather well, and achieve the effect of low cost, easy promotion and use, and luster and moisture
- Summary
- Abstract
- Description
- Claims
- Application Information
AI Technical Summary
Problems solved by technology
Method used
Examples
Embodiment 1
[0012] The leather finishing agent described in this embodiment has the following components: 60 parts of acrylate, 30 parts of chloroprene, 15 parts of acrylonitrile, 15 parts of styrene propylene, 5 parts of styrene propylene, 2 parts of acrylic acid, ammonium persulfate 0.8 parts, 2 parts of sodium lauryl sulfate, 2 parts of sodium lauryl sulfate, 2 parts of polyethylene oxide, 4.0 parts of sodium bisulfate, appropriate amount of ammonia water, appropriate amount of deionized water (general value: the ammonia water is 3 parts, deionized water is 10 parts), the above are all parts by mass.
[0013] The preparation method of the above-mentioned leather finishing agent is as follows: mix deionized water, sodium lauryl sulfate, polyethylene oxide, acrylate, acrylonitrile, and styrene according to the formula, keep stirring and emulsifying for 2 hours, then raise the temperature to 60°C for 1 hour , add ammonium persulfate, continue to heat up to 70°C, continue to react for 3 ho...
Embodiment 2
[0017] The leather finishing agent described in this embodiment is different from Example 1 in that each component is composed as follows: 55 parts of acrylate, 26 parts of chloroprene, 5 parts of acrylonitrile, 5 parts of styrene acrylic, 5 parts of styrene acrylic , 1 part of acrylic acid, 0.3 parts of ammonium persulfate, 1 part of sodium lauryl sulfate, 1 part of sodium lauryl sulfate, 1 part of polyethylene oxide, 0.01 part of sodium bisulfate, appropriate amount of ammonia water, appropriate amount of deionized water, the above All are parts by mass.
[0018] The leather finishing agent described in this embodiment, production and use method are the same as embodiment 1, and use effect can be comparable with it.
Embodiment 3
[0020] The leather finishing agent described in this embodiment is different from Example 1 in that each component is composed as follows: 57 parts of acrylate, 27 parts of chloroprene, 5 parts of acrylonitrile, 10 parts of styrene acrylic, 8 parts of styrene acrylic , 1 part of acrylic acid, 0.3 parts of ammonium persulfate, 1 part of sodium lauryl sulfate, 1 part to 2 parts of sodium lauryl sulfate, 1 part of polyethylene oxide, 0.01 part of sodium bisulfate, appropriate amount of ammonia water, deionized water Appropriate amount, all of the above are parts by mass.
PUM
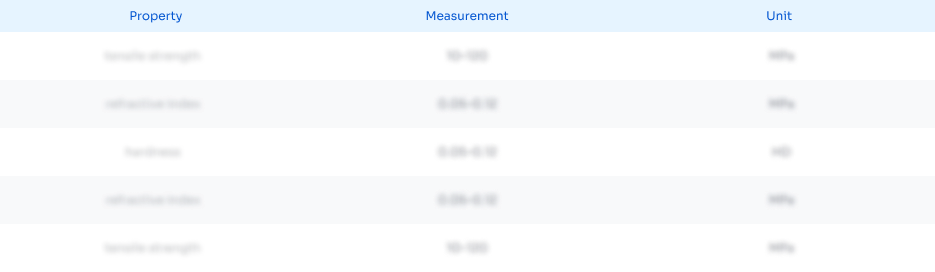
Abstract
Description
Claims
Application Information

- R&D
- Intellectual Property
- Life Sciences
- Materials
- Tech Scout
- Unparalleled Data Quality
- Higher Quality Content
- 60% Fewer Hallucinations
Browse by: Latest US Patents, China's latest patents, Technical Efficacy Thesaurus, Application Domain, Technology Topic, Popular Technical Reports.
© 2025 PatSnap. All rights reserved.Legal|Privacy policy|Modern Slavery Act Transparency Statement|Sitemap|About US| Contact US: help@patsnap.com