Preparation method of LCP film
A film and non-woven technology, applied in the field of LCP film preparation, can solve the problems of poor tensile strength and difficult film processing, and achieve the effects of increasing flexibility, good mechanical properties, and improving paper strength
- Summary
- Abstract
- Description
- Claims
- Application Information
AI Technical Summary
Problems solved by technology
Method used
Image
Examples
preparation example Construction
[0021] The present invention is specifically described below in conjunction with accompanying drawing, as figure 1 Shown, a kind of preparation method of LCP thin film mainly comprises the following steps:
[0022] Step 1. The raw material LCP chopped fibers are disintegrated and dispersed by a hydraulic pulper. The disintegration time is 20 minutes, and the concentration after disintegration is 0.3%;
[0023] Step 2, performing fiber surface treatment after step 1 to obtain slurry;
[0024] Step 3, filter and form the slurry through a paper machine with a speed of 7-20m / min. During the forming process, in order to ensure the uniformity of the non-woven fabric, add a certain amount of dispersant and defoamer, and then Drying in a dryer at 80-120°C to obtain LCP non-woven fabrics;
[0025] Step 4, melting the LCP non-woven fabric into a film to obtain an LCP film.
[0026] In the above-mentioned step 4, the melting film is specifically: firstly melt the LCP non-woven fabric ...
Embodiment 1
[0030] Configure slurry A:
[0031] Step 1. The LCP chopped fibers with a diameter of 20 μm and a length of 6 mm are disintegrated and dispersed by a hydraulic pulper. The disintegration time is 20 minutes, and the concentration after disintegration is 0.3%;
[0032] Step 2: After step 1, use a conical slag remover and a pressure screen purifier to screen and purify to obtain qualified slurry for use.
[0033] Configure slurry B:
[0034] Step 1. The LCP chopped fibers with a diameter of 40 μm and a length of 3 mm are disintegrated and dispersed by a hydraulic pulper. The disintegration time is 20 minutes, and the concentration after disintegration is 0.3%;
[0035] Step 2: After step 1, carry out fiber surface treatment, use ultrasonic circulation treatment for 16 minutes, ultrasonic power 80KW, until the fiber is completely divided into filaments, and then use conical slag remover and pressure screen purifier to screen and purify to obtain qualified slurry B standby.
[0...
Embodiment 2
[0039] Step 1. The LCP chopped fibers with a diameter of 40 μm and a length of 3 mm are disintegrated and dispersed by a hydraulic pulper. The disintegration time is 20 minutes, and the concentration after disintegration is 0.3%;
[0040] Step 2: After step 1, carry out fiber surface treatment, adopt ultrasonic circulation treatment for 8 minutes, and control the ultrasonic power at 90KW until the fiber is completely divided into filaments, and then use conical slag remover and pressure screen purifier to screen and purify to obtain qualified pulp material.
[0041] Step 3, filter the slurry obtained in step 2 through a paper machine with a vehicle speed of 12m / min. In the forming process, in order to ensure the uniformity of the nonwoven fabric, add a certain amount of dispersant and defoamer, and then Drying in a dryer at 120°C to obtain LCP non-woven fabrics;
[0042] Step 4: Melt the LCP non-woven fabric with low-temperature hot-pressing part through the hot roll first, a...
PUM
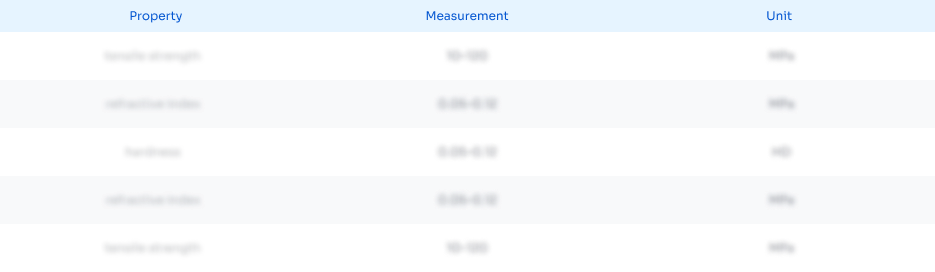
Abstract
Description
Claims
Application Information

- R&D
- Intellectual Property
- Life Sciences
- Materials
- Tech Scout
- Unparalleled Data Quality
- Higher Quality Content
- 60% Fewer Hallucinations
Browse by: Latest US Patents, China's latest patents, Technical Efficacy Thesaurus, Application Domain, Technology Topic, Popular Technical Reports.
© 2025 PatSnap. All rights reserved.Legal|Privacy policy|Modern Slavery Act Transparency Statement|Sitemap|About US| Contact US: help@patsnap.com