Raw material composition for preparing light-cured resin, light-cured resin prepared from raw material composition and application of light-cured resin
A raw material composition and technology of photocurable resin, which is applied in the field of curable resin synthesis, can solve the problems of reduced impact resistance, achieve low shrinkage, excellent mechanical properties and thermal properties, and increase the effect of crosslinking density
- Summary
- Abstract
- Description
- Claims
- Application Information
AI Technical Summary
Problems solved by technology
Method used
Image
Examples
Embodiment 1-5
[0060] The preparation of embodiment 1-5 light curing IPN resin
[0061] The preparation steps of light curing IPN resin are as follows:
[0062] 1. Ingredients process
[0063] The cyanate ester was dissolved in the photocurable prepolymer in beaker 1 and stirred at 60° C. for 10 minutes. Mix the catalyst and part of the diluent in beaker 2, pour into beaker 1 after ultrasonication for 30 minutes, rinse beaker 2 with the remaining diluent and pour into beaker 1, then add photoinitiator and stir for 10 minutes. Place the beaker 1 in a vacuum box, vacuumize for 10 minutes, and remove air bubbles for later use.
[0064] 2. Curing process
[0065] 1) UV curing: pour the mixture prepared by the above batching process into a mold, and irradiate for 200 seconds under a 400W UV light to obtain a preliminary cured product.
[0066] 2) Thermal curing: put the preliminary cured product in a temperature-programmed oven for stepwise heating and curing, rise to 90°C for 30 minutes, kee...
Embodiment 6
[0070] The performance test of embodiment 6 light-cured IPN resin
[0071] The photocurable IPN resin samples prepared in Examples 1-5 above were subjected to mechanical and thermal performance tests.
[0072] The tensile strength is measured on a universal mechanical performance testing machine according to the ISO527 standard; the glass transition temperature Tg is obtained from Tanδ on a dynamic thermomechanical analyzer DMA, the temperature range is 20-300°C, the heating rate is 3°C / min, and the vibration frequency is 1.0Hz. The sample size is 33mm×13mm×3.0mm; the heat distortion temperature is measured on a Vicat tester, and the sample size is 80mm×10mm×3.0mm.
[0073] Table 2 Properties of photocurable IPN resin
[0074]
[0075]
PUM
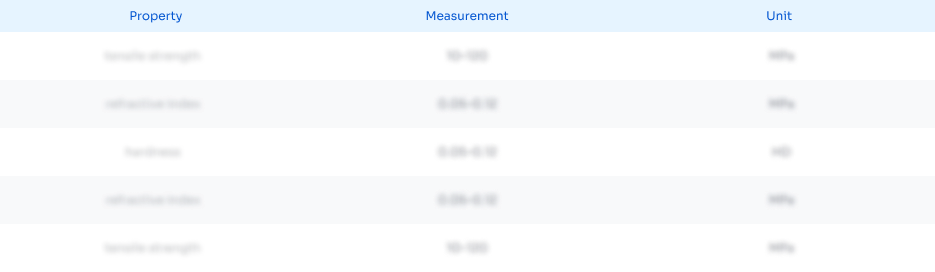
Abstract
Description
Claims
Application Information

- R&D
- Intellectual Property
- Life Sciences
- Materials
- Tech Scout
- Unparalleled Data Quality
- Higher Quality Content
- 60% Fewer Hallucinations
Browse by: Latest US Patents, China's latest patents, Technical Efficacy Thesaurus, Application Domain, Technology Topic, Popular Technical Reports.
© 2025 PatSnap. All rights reserved.Legal|Privacy policy|Modern Slavery Act Transparency Statement|Sitemap|About US| Contact US: help@patsnap.com