Aviation titanium alloy 3D printing enhancement process
A 3D printing and titanium alloy technology, applied in the field of aerospace titanium alloy 3D printing enhancement technology, can solve the problems of easy printing defects, heat concentration, large residual stress, etc.
- Summary
- Abstract
- Description
- Claims
- Application Information
AI Technical Summary
Problems solved by technology
Method used
Examples
Embodiment 1
[0021] A kind of aviation titanium alloy 3D printing enhancement process proposed by the present invention comprises the following steps:
[0022] S1. Flexible powder spreading: After the raw materials to be powdered are mixed by the mixer according to the required ratio, they are output through the output end of the mixer, and the mixed sample is spread on the powder bed through the scraper bar and the powder leakage groove to complete the flexible spreading. pink;
[0023] S2. Metal powder preheating: After the flexible powder spreading in step S1, the metal powder on the powder bed is scanned by laser for the first time, until the temperature of the metal powder laid on the powder bed rises to 120°C, the power is 60mW, and the scanning speed is 500mm / min, keep for 5min, then raise the temperature to 180°C to complete the preheating of the metal powder;
[0024] S3. Laser forming: plan the scanning path for the preheated metal powder layer in step S2 according to the set sc...
Embodiment 2
[0029] A kind of aviation titanium alloy 3D printing enhancement process proposed by the present invention comprises the following steps:
[0030] S1. Flexible powder spreading: After the raw materials to be powdered are mixed by the mixer according to the required ratio, they are output through the output end of the mixer, and the mixed sample is spread on the powder bed through the scraper bar and the powder leakage groove to complete the flexible spreading. pink;
[0031] S2. Metal powder preheating: after the flexible powder spreading in step S1, the metal powder on the powder bed is scanned by laser for the first time, until the temperature of the metal powder laid on the powder bed rises to 130°C, the power is 50mW, and the scanning speed is 550mm / min, keep for 4min, then raise the temperature to 200°C to complete the preheating of the metal powder;
[0032] S3. Laser forming: plan the scanning path for the preheated metal powder layer in step S2 according to the set sc...
Embodiment 3
[0037] A kind of aviation titanium alloy 3D printing enhancement process proposed by the present invention comprises the following steps:
[0038] S1. Flexible powder spreading: After the raw materials to be powdered are mixed by the mixer according to the required ratio, they are output through the output end of the mixer, and the mixed sample is spread on the powder bed through the scraper bar and the powder leakage groove to complete the flexible spreading. pink;
[0039] S2. Metal powder preheating: After the flexible powder spreading in step S1, the metal powder on the powder bed is scanned by laser for the first time, until the temperature of the metal powder laid on the powder bed rises to 140°C, the power is 30mW, and the scanning speed is 600mm / min, keep for 3min, then raise the temperature to 220°C to complete the preheating of the metal powder;
[0040] S3. Laser forming: plan the scanning path for the preheated metal powder layer in step S2 according to the set sc...
PUM
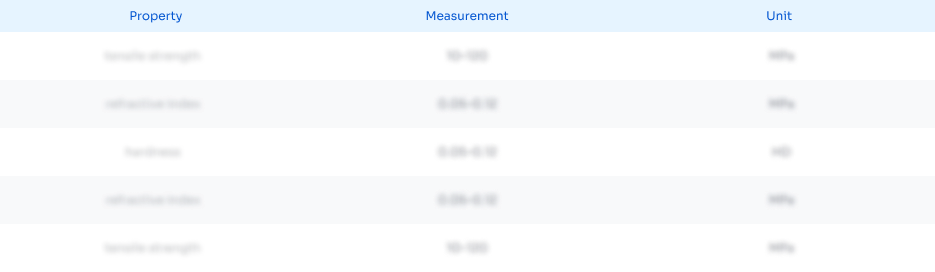
Abstract
Description
Claims
Application Information

- R&D
- Intellectual Property
- Life Sciences
- Materials
- Tech Scout
- Unparalleled Data Quality
- Higher Quality Content
- 60% Fewer Hallucinations
Browse by: Latest US Patents, China's latest patents, Technical Efficacy Thesaurus, Application Domain, Technology Topic, Popular Technical Reports.
© 2025 PatSnap. All rights reserved.Legal|Privacy policy|Modern Slavery Act Transparency Statement|Sitemap|About US| Contact US: help@patsnap.com