Preparation method of microcrystalline glass resistance paste
A technology of resistance paste and glass ceramics, which is applied in the direction of cable/conductor manufacturing, conductive materials dispersed in non-conductive inorganic materials, circuits, etc., can solve the problems of high preparation cost, many precious raw materials, and slow promotion speed. Achieve the effect of reducing production cost, reducing usage, and improving market competitiveness
- Summary
- Abstract
- Description
- Claims
- Application Information
AI Technical Summary
Problems solved by technology
Method used
Examples
Embodiment 1
[0023] A method for preparing a glass-ceramic resistance paste, the method comprising the following steps:
[0024] A. Material selection: select the required raw materials;
[0025] B. Drying: Put each raw material into a drying box for drying treatment;
[0026] C. Impurity removal: put each raw material into the impurity removal box for impurity removal treatment;
[0027] D, pulverization: put each raw material into pulverizer respectively and carry out pulverization treatment, and pulverization order number is 40 orders;
[0028] E. Grinding: Put the pulverized raw materials into a grinder for grinding, and the grinding mesh is 100 mesh;
[0029] F, mixing: put each raw material after grinding into the stirring dish according to parts by weight and carry out stirring process;
[0030] G. Binding and forming: put the mixed slurry into the three-roll rolling machine for binding;
[0031] H. Performance test: test the viscosity, rheology, silver content and thermal deter...
Embodiment 2
[0040] A method for preparing a glass-ceramic resistance paste, the method comprising the following steps:
[0041] A. Material selection: select the required raw materials;
[0042] B. Drying: Put each raw material into a drying box for drying treatment;
[0043] C. Impurity removal: put each raw material into the impurity removal box for impurity removal treatment;
[0044] D, pulverization: put each raw material into the pulverizer respectively and carry out pulverization treatment, and the pulverization mesh number is 80 mesh;
[0045] E. Grinding: Put the pulverized raw materials into a grinder for grinding, and the grinding mesh is 150 mesh;
[0046] F, mixing: put each raw material after grinding into the stirring dish according to parts by weight and carry out stirring process;
[0047] G. Binding and forming: put the mixed slurry into the three-roll rolling machine for binding;
[0048] H. Performance test: test the viscosity, rheology, silver content and thermal ...
Embodiment 3
[0057] A method for preparing a glass-ceramic resistance paste, the method comprising the following steps:
[0058] A. Material selection: select the required raw materials;
[0059] B. Drying: Put each raw material into a drying box for drying treatment;
[0060] C. Impurity removal: put each raw material into the impurity removal box for impurity removal treatment;
[0061] D, pulverization: put each raw material into pulverizer respectively and carry out pulverization treatment, and pulverization mesh number is 100 mesh;
[0062] E. Grinding: Put the pulverized raw materials into a grinder for grinding, and the grinding mesh is 200 mesh;
[0063] F, mixing: put each raw material after grinding into the stirring dish according to parts by weight and carry out stirring process;
[0064] G. Binding and forming: put the mixed slurry into the three-roll rolling machine for binding;
[0065] H. Performance test: test the viscosity, rheology, silver content and thermal deterio...
PUM
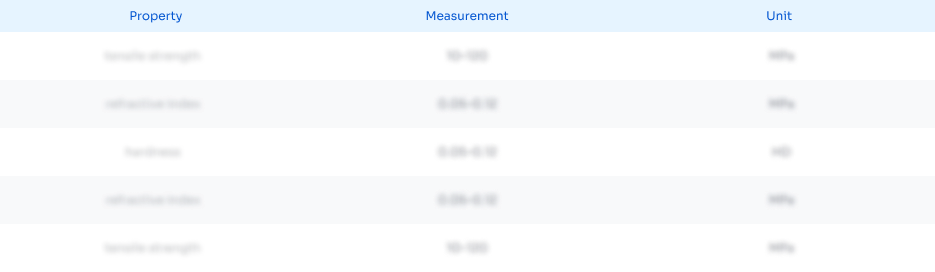
Abstract
Description
Claims
Application Information

- Generate Ideas
- Intellectual Property
- Life Sciences
- Materials
- Tech Scout
- Unparalleled Data Quality
- Higher Quality Content
- 60% Fewer Hallucinations
Browse by: Latest US Patents, China's latest patents, Technical Efficacy Thesaurus, Application Domain, Technology Topic, Popular Technical Reports.
© 2025 PatSnap. All rights reserved.Legal|Privacy policy|Modern Slavery Act Transparency Statement|Sitemap|About US| Contact US: help@patsnap.com