High-thermal-conductivity rubber nano composite material and preparation method thereof
A composite material and rubber nanotechnology, applied in the rubber field, can solve problems such as unfavorable thermal conductivity of materials, unfavorable filler network, etc., and achieve the effects of easy mass production, simple operation and low energy consumption
- Summary
- Abstract
- Description
- Claims
- Application Information
AI Technical Summary
Problems solved by technology
Method used
Image
Examples
Embodiment 1
[0056] The specific formula is as follows:
[0057] Each component is calculated in parts by weight,
[0058]
[0059] The specific implementation process is as follows:
[0060] Stir and ultrasonically mix 100ml of graphene oxide aqueous dispersion with a concentration of 2mg / ml (adjusted by ammonia water to pH=10.5) and 100ml of nano-alumina aqueous dispersion with a concentration of 50mg / ml, and then add 2 grams of ascorbic acid and 0.05 grams of Triton X-100 emulsifier, 16.67 grams of natural rubber latex (60%wt of rubber content), 0.05 gram of sulfur water dispersion (20%wt of sulfur content), 0.2 gram of zinc oxide water dispersion (20%wt of zinc oxide content), 0.1 gram of accelerator D aqueous dispersion (promoting D content 20%wt), 0.2 gram of antioxidant AW aqueous dispersion (AW content 20%wt), etc. were stirred evenly. The uniformly stirred slurry was sealed and placed in a blast drying oven at 90°C for 2 hours to obtain a hydrogel. The second step: the obtai...
Embodiment 2
[0062] The specific formula is as follows:
[0063] Each component is calculated in parts by weight,
[0064]
[0065]
[0066] The specific implementation process is as follows:
[0067] 100ml concentration of 10mg / ml graphene oxide aqueous dispersion (ammonia water to adjust its pH=8) and 100ml concentration of 100mg / ml nano-zinc oxide aqueous dispersion were stirred and ultrasonically mixed evenly, followed by adding 2 grams of ethylenediamine, 0.5 Gram sorbitan fatty acid ester emulsifier, 16.67 gram styrene-butadiene rubber latex (containing 60%wt of rubber content), 0.05 gram sulfur aqueous dispersion (sulfur content 20%wt), 0.2 gram zinc oxide aqueous dispersion (zinc oxide Content 20%wt), 0.1 gram accelerator D water dispersion (promote D content 20%wt), 0.2 gram anti-aging agent AW water dispersion (AW content 20%wt), etc. Stir evenly. The uniformly stirred slurry was sealed and placed in an air-blast drying oven at 80°C for reduction for 6 hours to obtain a h...
Embodiment 3
[0069] The specific formula is as follows:
[0070] Each component is calculated in parts by weight,
[0071]
[0072]
[0073] The specific implementation process is as follows:
[0074] 100ml concentration is 10mg / ml graphene oxide aqueous dispersion (ammonia water adjusts its PH=11) and 100ml concentration is 150mg / ml carbon nanotube aqueous dispersion liquid stirring, ultrasonic mixing is uniform, add 4 grams of ascorbic acid successively, 1 gram loses Sorbitan fatty acid ester polyoxyethylene ether emulsifier, 16.67 grams of nitrile rubber latex (containing 60%wt of glue), 0.05 gram of sulfur water dispersion (sulfur content 20%wt), 0.2 gram of zinc oxide water dispersion ( Zinc oxide content 20%wt), 0.1 gram accelerator D water dispersion (promote D content 20%wt), 0.2 gram anti-aging agent AW water dispersion (AW content 20%wt) etc. Stir evenly. The uniformly stirred slurry was sealed and placed in a blast drying oven at 70°C for reduction for 6 hours to obtain ...
PUM
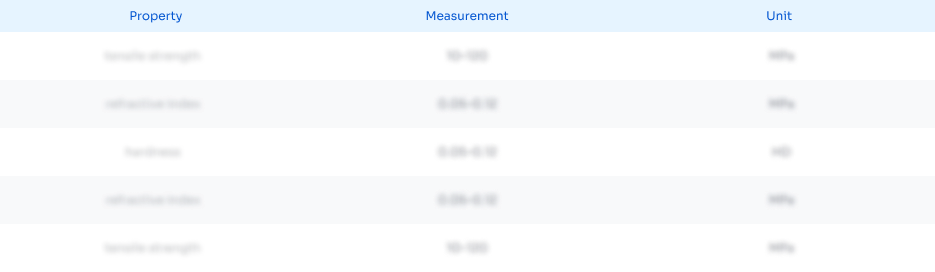
Abstract
Description
Claims
Application Information

- Generate Ideas
- Intellectual Property
- Life Sciences
- Materials
- Tech Scout
- Unparalleled Data Quality
- Higher Quality Content
- 60% Fewer Hallucinations
Browse by: Latest US Patents, China's latest patents, Technical Efficacy Thesaurus, Application Domain, Technology Topic, Popular Technical Reports.
© 2025 PatSnap. All rights reserved.Legal|Privacy policy|Modern Slavery Act Transparency Statement|Sitemap|About US| Contact US: help@patsnap.com