FG-coated MOF composite material, coating containing composite material, and preparation methods and application of coating
A technology of composite materials and composite coatings, applied in the direction of anti-corrosion coatings, epoxy resin coatings, coatings, etc., to achieve the effect of improving the protective performance
- Summary
- Abstract
- Description
- Claims
- Application Information
AI Technical Summary
Problems solved by technology
Method used
Image
Examples
Embodiment 1
[0027] Preparation of FG@ZIF-8 modified epoxy resin composite coating includes the following steps:
[0028] (1) Preparation of FG@ZIF-8 composite material: Disperse 0.117g of FG in anhydrous methanol, oscillate ultrasonically for 2-3 hours, and then add 0.5g of Zn(NO 3 ) 2 ·6H 2 O and 0.55g of 2-methylimidazole were added to the FG methanol dispersion, stirred for 2 hours to obtain a suspension, which was separated by centrifugation and washed alternately with methanol and deionized water for 4 times, and finally dried at 60°C for 12 hours to obtain a powder In this example, the molar ratio of zinc ions to 2-methylimidazole is 1:4, and the mass fraction of FG in all the raw materials participating in the reaction is 10%.
[0029] (2) Preparation of composite coating: mix epoxy resin, FG@ZIF-8 and diluent with a mass ratio of 10:0.5:8, wherein the diluent is a mixture of xylene and n-butanol, and xylene and n-butanol The mass ratio is 2:1; the ball mill is stirred for 0.5h,...
Embodiment 2
[0040] Preparation of FG@ZIF-7 modified epoxy resin composite coating includes the following steps:
[0041] (1) Preparation of FG@ZIF-7 composite material: Disperse 0.233g FG in anhydrous methanol, ultrasonically shake for 2-3h, and then add 0.5g ZnCl 2 and 0.433g of benzimidazole were added to the FG methanol dispersion, stirred for 2 hours to obtain a suspension, which was separated by centrifugation and washed alternately with methanol and deionized water for 4 times, and finally dried at 60°C for 12 hours to obtain powdered FG @MOF composite material, in this example, the molar ratio of zinc ions to benzoimidazole is 1:1, and the mass fraction of FG in all the raw materials participating in the reaction is 20%;
[0042] (2) Preparation of composite coating: mix epoxy resin, FG@ZIF-7 and diluent with a mass ratio of 10:2:10, wherein the diluent is a mixture of xylene and n-butanol, and xylene and n-butanol The mass ratio is 3:1; the ball mill is stirred for 0.5h, and then...
Embodiment 3
[0046] The preparation of aminated FG@ZIF-8 modified epoxy resin composite coating includes the following steps:
[0047] (1) Preparation of aminated FG@ZIF-8 composite material: Disperse 0.8g FG in anhydrous methanol, oscillate ultrasonically for 2-3h, then add 0.5g Zn(NO 3 ) 2 ·6H 2 O, 0.3g 2-methylimidazole and 0.4g 2-aminobenzimidazole were added to the FG methanol dispersion, stirred for 2h to obtain a suspension, which was centrifuged and washed 4 times alternately with methanol and deionized water, and finally in Dry at 60°C for 12 hours to obtain a powdered aminated FG@ZIF-8 composite material. In this example, the molar ratio of zinc ions to imidazole ligands is 1:4, and the mass fraction of FG in all the raw materials participating in the reaction is 40. %;
[0048] (2) Preparation of composite coating: mix epoxy resin, aminated FG@ZIF-8 and diluent with a mass ratio of 10:0.3:2, wherein the diluent is a mixture of xylene and n-butanol, and xylene and n-butanol T...
PUM
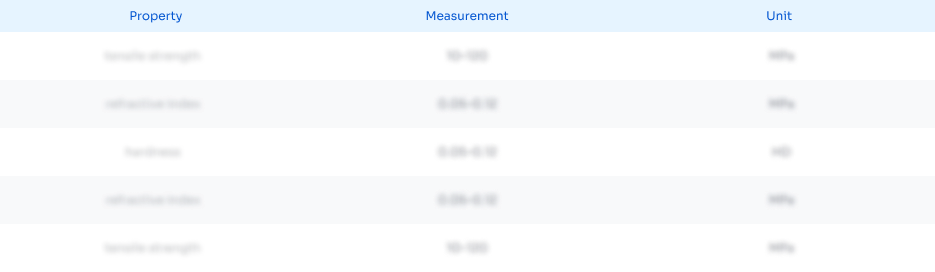
Abstract
Description
Claims
Application Information

- R&D
- Intellectual Property
- Life Sciences
- Materials
- Tech Scout
- Unparalleled Data Quality
- Higher Quality Content
- 60% Fewer Hallucinations
Browse by: Latest US Patents, China's latest patents, Technical Efficacy Thesaurus, Application Domain, Technology Topic, Popular Technical Reports.
© 2025 PatSnap. All rights reserved.Legal|Privacy policy|Modern Slavery Act Transparency Statement|Sitemap|About US| Contact US: help@patsnap.com