Preparation method of composite iron-carbon sintered ore and blast furnace smelting process
A technology for sinter and iron carbon, which is applied in the preparation of composite iron carbon sinter, blast furnace ironmaking process, and the preparation and application of composite sinter, and can solve the problem of uneven particle distribution, uneven distribution of gas in the furnace, and distribution in the chute. Serious segregation and other problems, to achieve the effect of shortening the process flow, eliminating the coking process, and avoiding easy segregation
- Summary
- Abstract
- Description
- Claims
- Application Information
AI Technical Summary
Problems solved by technology
Method used
Image
Examples
Embodiment 1
[0058] Such as figure 2 Shown, a kind of preparation method of composite iron-carbon sinter, the method comprises the following steps:
[0059] 1) Batching and mixing: batching iron ore and coal, adding flux to the batching, mixing the prepared materials to obtain a sintering mixture;
[0060] 2) Granulation: the sintered mixture is granulated and pelletized to obtain sintered green pellets;
[0061] 3) Microwave sintering: Microwave sintering is used after the sintered green balls are distributed, in which the volatile matter and crystal water in the sintered green balls are decomposed and volatilized, and the fixed carbon particles in the iron ore and coal are broken and recrystallized to obtain high-strength composite iron-carbon sintering mine.
[0062] Wherein, the composite iron-carbon sintered ore obtained in step 3) also includes a silicate binder phase. The microwave sintering described in step 3) specifically includes: adopting multiple microwave sources, and hea...
Embodiment 2
[0064] Repeat Example 1, except that step 3) also includes the step of cooling the sintered ore, specifically: after microwave sintering, nitrogen gas is introduced to cool the composite iron-carbon sintered ore.
Embodiment 3
[0066] Repeat Example 2, except that the microwave sintering described in step 3) is carried out in an oxygen-free or weakly oxygen-enclosed environment, specifically: nitrogen gas is introduced, and the microwave sintering is carried out in a nitrogen-protected environment. Wherein, the oxygen concentration in the sintering system is lower than 10%.
PUM
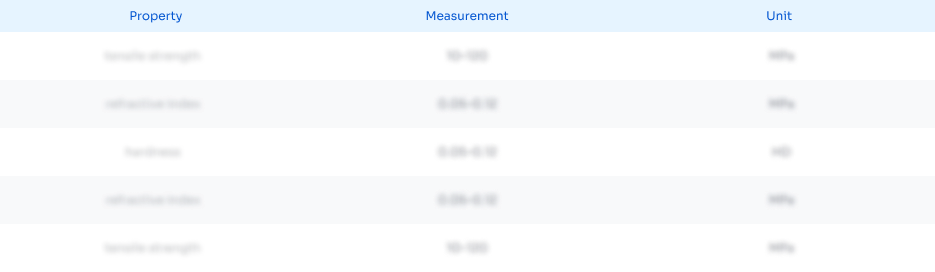
Abstract
Description
Claims
Application Information

- R&D Engineer
- R&D Manager
- IP Professional
- Industry Leading Data Capabilities
- Powerful AI technology
- Patent DNA Extraction
Browse by: Latest US Patents, China's latest patents, Technical Efficacy Thesaurus, Application Domain, Technology Topic, Popular Technical Reports.
© 2024 PatSnap. All rights reserved.Legal|Privacy policy|Modern Slavery Act Transparency Statement|Sitemap|About US| Contact US: help@patsnap.com