Method for pretreating wood fiber raw material by using deep eutectic solvent and deep eutectic solvent used by method
A lignocellulosic raw material, low eutectic solvent technology, applied in biofuels, fermentation and other directions, can solve the problems of complex hydrogen bond donor synthesis path, achieve easy separation and downstream utilization, avoid polycondensation reaction, improve specific surface area and pore size rate effect
- Summary
- Abstract
- Description
- Claims
- Application Information
AI Technical Summary
Problems solved by technology
Method used
Image
Examples
Embodiment 1
[0026] 1) The molar ratio of choline chloride to guaiacol is 1:2, and the molar ratio of choline chloride, guaiacol and aluminum chloride in the experimental group added with aluminum chloride is 62:124:1 . The system was first heated at 80°C until a homogeneous, clear solvent was obtained.
[0027] 2) Mix the wheat straw with the deep eutectic solvent at a mass ratio of 1:10, and react at 80-130°C for 60 minutes. After pretreatment, separate the solid and liquid to obtain the pretreatment material and the pretreatment liquid containing lignin. The pretreatment material After washing with ethanol, wash with distilled water until the washing solution is clear.
[0028] The influence of the eutectic system with and without adding aluminum chloride on the recovery of wheat straw components, the results show that in the pretreatment system without adding aluminum chloride, with the increase of temperature, the recovery of pretreated materials is in the About 95%; And in the expe...
Embodiment 2
[0030] Weigh 1g of pretreated material (dry matter), put it in a hydrolysis bottle, add 1mL of 1M acetic acid-sodium acetate buffer solution, and then add cellulase 25FPU / g dextran, xylanase 150U / g xylan Enzyme preparation, add distilled water at last to make the system solids concentration 5%. Then the hydrolysis bottle was placed in a shaker at 50° C. and 150 rpm for enzymolysis for 72 hours. After enzymatic hydrolysis, centrifuge, analyze the concentration of glucose and xylose in the supernatant of enzymatic hydrolysis, and calculate the yield of enzymatic hydrolysis, the results are as follows: image 3 , Figure 4 shown.
[0031] The results showed that the hydrolysis yields of glucan and xylanase in the pretreatment system without adding aluminum chloride remained stable with the change of temperature, about 50% and 20%, respectively. However, in the pretreatment system with the addition of aluminum chloride, as the pretreatment temperature increased, the enzymatic h...
Embodiment 3
[0033] An appropriate amount of distilled water is added to the pretreatment liquid collected in the above pretreatment, the lignin dissolved therein is precipitated and centrifuged, and the lignin is freeze-dried to obtain a lignin powder. The molecular weight of the obtained lignin powder was determined by gel permeation chromatography, and the results are shown in Table 1.
[0034] Table 1 Molecular weight of lignin dissolved in eutectic pretreatment process
[0035] CEL 80℃ 90℃ 100℃ 110℃ 120℃ 130℃ m w (Da)
[0036]It can be seen from Table 1 that the molecular weight of lignin in wheat straw is as high as 14654Da. After pretreatment with deep eutectic solvent, the molecular weight of lignin dissolved was greatly reduced, from 14654Da to 2630Da (80℃), 2432Da (90℃), 2231Da (100℃), 1866Da (110℃) and 1542Da (120℃). ), indicating that the degraded lignin mostly exists in the form of small molecules. When the pretreatment temperature further increased ...
PUM
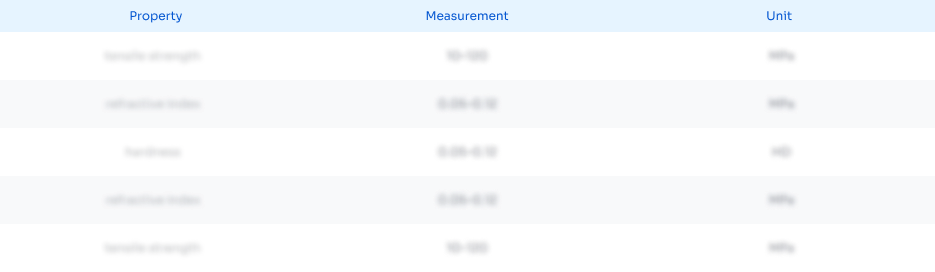
Abstract
Description
Claims
Application Information

- Generate Ideas
- Intellectual Property
- Life Sciences
- Materials
- Tech Scout
- Unparalleled Data Quality
- Higher Quality Content
- 60% Fewer Hallucinations
Browse by: Latest US Patents, China's latest patents, Technical Efficacy Thesaurus, Application Domain, Technology Topic, Popular Technical Reports.
© 2025 PatSnap. All rights reserved.Legal|Privacy policy|Modern Slavery Act Transparency Statement|Sitemap|About US| Contact US: help@patsnap.com