Method for continuous drying of hexamethylolmelamine
A technology of hexamethylolmelamine and hexamethylolmelamine paste, which is applied in the field of continuous drying of hexamethylolmelamine, can solve the problem of low drying efficiency, polycondensation of hexamethylolmelamine materials, and affecting the degree of methylolation of products Retention rate and other issues, to achieve stable product quality, good technical effect, and shorten the drying time
- Summary
- Abstract
- Description
- Claims
- Application Information
AI Technical Summary
Problems solved by technology
Method used
Image
Examples
Embodiment 1
[0020] Continuously divert the undried hexamethylolmelamine paste material through six screw pumps into the belt vacuum dryer and evenly distribute the material on the drying belt. The temperature is 75°C, drying for 50min obtains material I, the material I passes through heating zone 2, wherein the steam temperature is 110°C, drying for 50min obtains material II, and then passes through heating zone 3, wherein the hot water temperature is 45°C, and the powder is ground after drying for 50min. The hexamethylolmelamine powder III was obtained, and the vacuum degree in the dryer was -0.099Mpa during the whole drying process.
Embodiment 2 to 4
[0022] Example 2 to Example 4 were carried out according to the steps of Example 1, and the only difference was the index parameter of the paste material, the temperature of the heating medium and the heating time. For details, see Table 1. The prepared hexamethylol The quality inspection data of melamine powder are shown in Table 4.
[0023] Table 1 Reaction parameters of Example 1 to Example 4
[0024] Process parameters Example 1 Example 2 Example 3 Example 4 Heating zone 1 medium hot water hot water hot water hot water Heating zone 1 medium temperature (℃) 75 60 90 70 Drying time of heating zone 1 (min) 50 60 45 70 Heating zone 2 medium steam steam steam steam Heating zone 2 medium temperature (℃) 110 100 120 105 Drying time of heating zone 2 (min) 50 60 45 70 Heating zone 3 medium hot water hot water hot water hot water Heating zone 3 medium temperature (℃) 45 30 60 40 ...
Embodiment 5 to Embodiment 8
[0026] Example 5 to Example 8 were carried out according to the steps of Example 1, and the only difference was the index parameter of the paste material, the temperature of the heating medium and the heating time. For details, see Table 2. The prepared hexamethylol The quality inspection data of melamine powder are shown in Table 4.
[0027] Table 2 Reaction parameters of Example 5 to Example 8
[0028] Process parameters Example 5 Example 6 Example 7 Example 8 Heating zone 1 medium hot water hot water hot water hot water Heating zone 1 medium temperature (℃) 80 75 85 65 Drying time of heating zone 1 (min) 40 55 60 65 Heating zone 2 medium steam steam steam steam Heating zone 2 medium temperature (℃) 110 115 110 105 Drying time of heating zone 2 (min) 40 55 60 65 Heating zone 3 medium hot water hot water hot water hot water Heating zone 3 medium temperature (℃) 40 50 50 55 ...
PUM
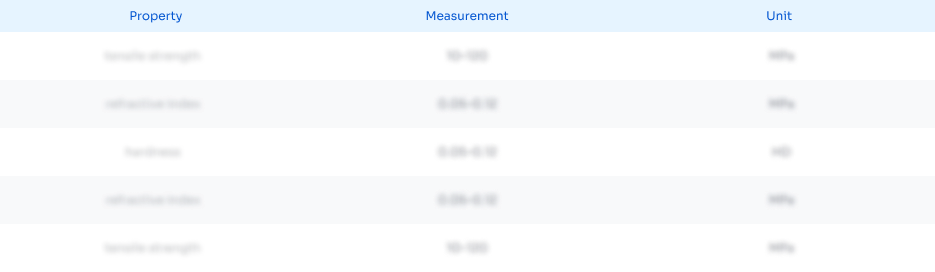
Abstract
Description
Claims
Application Information

- Generate Ideas
- Intellectual Property
- Life Sciences
- Materials
- Tech Scout
- Unparalleled Data Quality
- Higher Quality Content
- 60% Fewer Hallucinations
Browse by: Latest US Patents, China's latest patents, Technical Efficacy Thesaurus, Application Domain, Technology Topic, Popular Technical Reports.
© 2025 PatSnap. All rights reserved.Legal|Privacy policy|Modern Slavery Act Transparency Statement|Sitemap|About US| Contact US: help@patsnap.com