Method for producing high-iron sulphoaluminate cement by using red mud and aluminum ash
A high-iron sulfoaluminate and red mud technology, applied in the field of special cement, can solve the problems of large-scale equipment, human and environmental hazards, and toxic substance residues, so as to avoid scarring of the flue, improve erosion, and increase strength Effect
- Summary
- Abstract
- Description
- Claims
- Application Information
AI Technical Summary
Problems solved by technology
Method used
Image
Examples
Embodiment 1
[0050] (1) Pretreatment of waste sulfuric acid: after mixing 5.91 kg of calcium carbide slag with a water content of 10% and 20 kg of waste sulfuric acid with a water content of 68%, drying to a moisture content of 3 wt%, to obtain 14.6 kg of calcium sulfate-containing waste residue for use;
[0051] (2) Preparation of cement clinker: mix 5.5kg of sintering red mud, 3.5kg of secondary aluminum ash, 0.5kg of spent cathode carbon block, 2.5kg of waste residue containing calcium sulfate, and 4.5kg of limestone, and dry until the moisture content is lower than 5 wt%, ground to 80 μm sieve residue less than 10%, to obtain cement raw meal, calcined cement raw meal at 1250 ° C for 45 minutes, air cooled to 300 ° C and then naturally cooled to room temperature to obtain cement clinker;
[0052] (3) Prepare the mixture: sintering red mud was calcined at 750°C for 40 minutes and cooled rapidly to obtain modified red mud; the modified red mud and fluorogypsum were mixed at a mass ratio of...
Embodiment 2
[0055] (1) Pretreatment of waste sulfuric acid: after mixing 5.91 kg of calcium carbide slag with a water content of 10% and 20 kg of waste sulfuric acid with a water content of 68%, drying to a moisture content of 3 wt%, to obtain 14.6 kg of calcium sulfate-containing waste residue for use;
[0056] (2) Preparation of cement clinker: mix 6.0kg of Bayer process red mud, 2.5kg of secondary aluminum ash, 0.6kg of spent cathode carbon block, 2.3kg of waste residue containing calcium sulfate, and 6.5kg of limestone, and dry until the moisture content is lower than 5 wt%, ground to 80 μm sieve residue less than 10%, to obtain cement raw meal, calcined cement raw meal at 1280°C for 1 hour, air cooled to 300°C, and then naturally cooled to room temperature to obtain cement clinker;
[0057] (3) Prepare the mixture: sintering red mud was calcined at 750°C for 40 minutes and cooled rapidly to obtain modified red mud; the modified red mud and phosphogypsum were mixed at a mass ratio of 1...
Embodiment 3
[0060] (1) Preparation of cement clinker: mix 5kg sintering red mud, 3kg secondary aluminum ash, 0.5kg waste cathode carbon block, 2kg fluorogypsum, and 3kg limestone, dry until the moisture content is lower than 5wt%, and grind to 80 μm sieve The balance is less than 10% to obtain cement raw meal, calcining the cement raw meal at 1250°C for 50 minutes, air cooling to 300°C and then naturally cooling down to room temperature to obtain cement clinker;
[0061] (2) Prepare the mixture: sintering red mud was calcined at 750°C for 40 minutes and cooled rapidly to obtain modified red mud; the modified red mud, fluorogypsum, and limestone were mixed in a mass ratio of 10:3:2 to obtain mix B;
[0062] (3) Preparation of cement: mix cement clinker and mixture B at a mass ratio of 10:4, grind until the sieve residue of 80 μm is less than 10%, and obtain high iron sulfoaluminate cement.
PUM
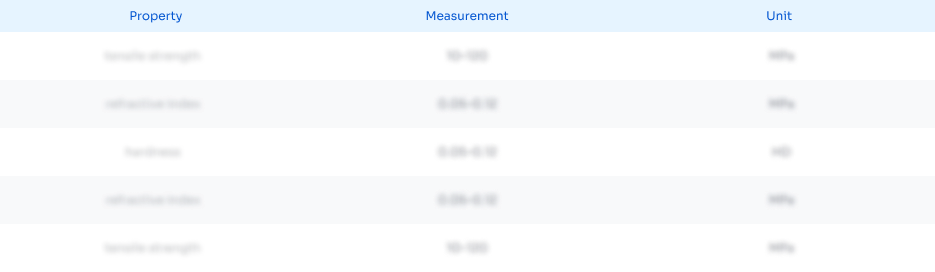
Abstract
Description
Claims
Application Information

- R&D
- Intellectual Property
- Life Sciences
- Materials
- Tech Scout
- Unparalleled Data Quality
- Higher Quality Content
- 60% Fewer Hallucinations
Browse by: Latest US Patents, China's latest patents, Technical Efficacy Thesaurus, Application Domain, Technology Topic, Popular Technical Reports.
© 2025 PatSnap. All rights reserved.Legal|Privacy policy|Modern Slavery Act Transparency Statement|Sitemap|About US| Contact US: help@patsnap.com