Industrial kiln waste heat recovery device
A waste heat recovery device and waste heat recovery technology, applied in furnaces, waste heat treatment, furnace components, etc., can solve problems such as increased production costs, environmental pollution, waste of resources, etc., and achieve reduced pollution, high heat recovery efficiency, and improved thermal efficiency. Effect
- Summary
- Abstract
- Description
- Claims
- Application Information
AI Technical Summary
Problems solved by technology
Method used
Image
Examples
Embodiment 1
[0041] see Figure 1-7 An industrial kiln 8 waste heat recovery device, which includes an industrial kiln 8 and a waste heat recovery box 21, a first heat pipe 11 is connected between the industrial kiln 8 and the waste heat recovery box 21, and the outer end of the first heat pipe 11 is fixed The heat insulation layer 12 is connected, so that when the heat in the hot exhaust gas in the industrial kiln 8 is introduced into the waste heat recovery box 21 through the first heat conduction pipe 11, the heat is not easily dissipated to the external environment due to the setting of the heat insulation layer 12 , in specific implementation, a primary filter structure can be installed at a suitable position in the first heat transfer pipe 11, so that the waste gas can be pre-filtered before entering the waste heat recovery box 21, and the harmful gas in the waste gas can be removed more effectively with the filter in the clean room .
[0042] A controller 9 is installed on the uppe...
PUM
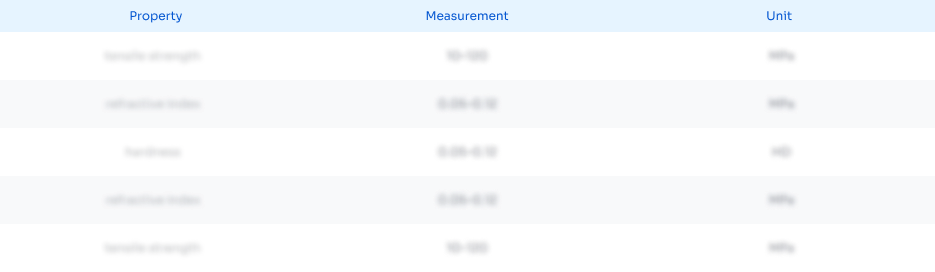
Abstract
Description
Claims
Application Information

- R&D
- Intellectual Property
- Life Sciences
- Materials
- Tech Scout
- Unparalleled Data Quality
- Higher Quality Content
- 60% Fewer Hallucinations
Browse by: Latest US Patents, China's latest patents, Technical Efficacy Thesaurus, Application Domain, Technology Topic, Popular Technical Reports.
© 2025 PatSnap. All rights reserved.Legal|Privacy policy|Modern Slavery Act Transparency Statement|Sitemap|About US| Contact US: help@patsnap.com