A kind of high tenacity petg material and its application
A high toughness and toughening technology, applied in the field of PETG, can solve the problems of reducing material transparency, poor fluidity, and improving water absorption of materials
- Summary
- Abstract
- Description
- Claims
- Application Information
AI Technical Summary
Problems solved by technology
Method used
Image
Examples
Embodiment 1
[0047] 70g of polymerized monomer (1), 120g of polymerized monomer (3), 200g of polymerized monomer (5), 2g of di-tert-butyl peroxide were added to 400g of toluene, and added dropwise to the reactor at a uniform speed at 110 °C, The dropping time is 7 hours, after the dropping is completed, the temperature is kept for 2 hours and the material is discharged, and the toughened polymer is obtained after the solvent is removed by rotary evaporation.
[0048] Its molecular weight was measured by gel permeation chromatography, Mw=123998.
[0049] 100 parts of PETG material (the molar ratio of ethylene glycol and 1,4 cyclohexanedimethanol is 5:5), 2 parts of the above toughening polymer, 0.2 part of antioxidant 1010, 0.4 part of lubricant Honeywell Add polyethylene wax 400A to the high-speed mixer, and stir at 600 rpm for at least 20 minutes until the stirring is uniform. The material was fed into a twin-screw extruder, and the extrusion temperature was 230° C. to obtain master batc...
Embodiment 2
[0051] 110g of polymerized monomer (2), 300g of polymerized monomer (5), and 1.5g of di-tert-butyl peroxide were added to 400g of toluene, and added dropwise to the reactor at a constant speed at 110 °C for 7 hours. After the dropping is completed, the material is kept for 2 hours and discharged, and the toughened polymer is obtained after the solvent is removed by rotary evaporation.
[0052] Its molecular weight was measured by gel permeation chromatography, Mw=157662.
[0053] 100 parts of PETG material with a weight average molecular weight of about 250,000 (the molar ratio of ethylene glycol and 1,4 cyclohexanedimethanol is 5:5), 3 parts of the above toughening polymer, 0.3 part of antioxidant 626, Add 0.4 part of lubricant pentaerythritol stearate to the high-speed mixer, and stir at 600 rpm for at least 20 minutes until the mixture is uniform. The material was fed into a twin-screw extruder, and the extrusion temperature was 230° C. to obtain master batches.
Embodiment 3
[0055] 150g of polymerized monomer (1), 100g of polymerized monomer (2), 150g of polymerized monomer (4) and 1.7g of di-tert-butyl peroxide were added to 400g of toluene, and added dropwise to the reactor at a uniform speed at 110°C, The dropping time is 7 hours, after the dropping is completed, the temperature is kept for 2 hours and the material is discharged, and the toughened polymer is obtained after the solvent is removed by rotary evaporation.
[0056] Its molecular weight was measured by gel permeation chromatography, Mw=137792.
[0057] 100 parts of PETG material with a weight average molecular weight of about 250,000 (the molar ratio of ethylene glycol and 1,4 cyclohexanedimethanol is 5:5), 5 parts of the above toughening polymer, 0.3 part of antioxidant 1029, Add 0.5 part of the lubricant magnesium stearate to the high-speed mixer, and mix at 600 rpm for at least 20 minutes until the mixing is uniform. The material was fed into a twin-screw extruder, and the extrus...
PUM
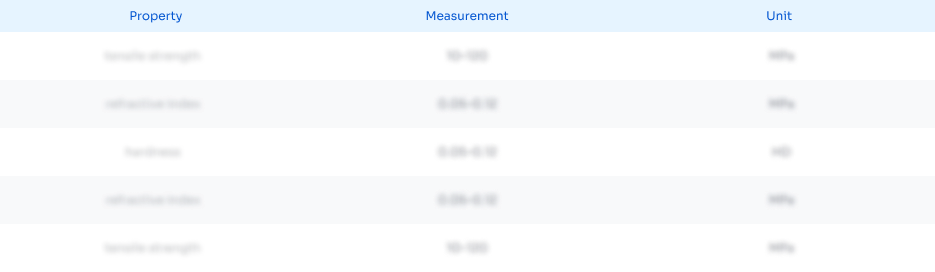
Abstract
Description
Claims
Application Information

- R&D Engineer
- R&D Manager
- IP Professional
- Industry Leading Data Capabilities
- Powerful AI technology
- Patent DNA Extraction
Browse by: Latest US Patents, China's latest patents, Technical Efficacy Thesaurus, Application Domain, Technology Topic, Popular Technical Reports.
© 2024 PatSnap. All rights reserved.Legal|Privacy policy|Modern Slavery Act Transparency Statement|Sitemap|About US| Contact US: help@patsnap.com