An Integral Axial Texture Grinder for Ultrasonic Vibration Cylindrical Fatigue Samples
A fatigue sample and ultrasonic vibration technology, which is used in grinding machine parts, preparation and sampling of test samples, etc., can solve the problem that the quality of surface processing affects the performance of workpieces, the reliability of machinery and equipment, and the inability to effectively remove the surface of shaft parts. Processing texture, uncontrollable grinding speed consistency, etc., to achieve the effect of improved processing accuracy, stable pressure, and reduced surface roughness value
- Summary
- Abstract
- Description
- Claims
- Application Information
AI Technical Summary
Problems solved by technology
Method used
Image
Examples
Embodiment Construction
[0022] The following will clearly and completely describe the technical solutions in the embodiments of the present invention with reference to the accompanying drawings in the embodiments of the present invention. Obviously, the described embodiments are only some, not all, embodiments of the present invention.
[0023] see Figure 1 to Figure 4 , the present invention provides a technical solution: an ultrasonic vibration cylindrical fatigue specimen integral type axial texture grinding machine, comprising an ultrasonic generator 1 and a workbench 27, the top of the workbench 27 is fixedly connected with a bracket 24 through a connecting bolt 25 , the top of the bracket 24 is provided with a guide rail 14, the guide rail 14 includes a slider guide rail and a mechanism guide rail, the slider guide rail and the mechanism guide rail are connected to each other by bolts, the slider 21 is movable on the top of the slider guide rail, and the top movable card of the mechanism guide ...
PUM
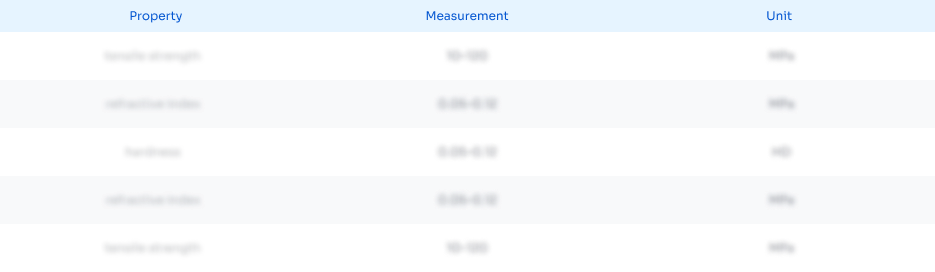
Abstract
Description
Claims
Application Information

- R&D Engineer
- R&D Manager
- IP Professional
- Industry Leading Data Capabilities
- Powerful AI technology
- Patent DNA Extraction
Browse by: Latest US Patents, China's latest patents, Technical Efficacy Thesaurus, Application Domain, Technology Topic, Popular Technical Reports.
© 2024 PatSnap. All rights reserved.Legal|Privacy policy|Modern Slavery Act Transparency Statement|Sitemap|About US| Contact US: help@patsnap.com