Heating furnace flue gas waste heat recovery system and combustion system
A flue gas waste heat and recovery system technology, which is applied in the direction of combustion methods, lighting and heating equipment, furnaces, etc., can solve the problem that the latent heat of condensation of flue gas cannot be recovered, the low-temperature sensible heat and latent heat of condensation of flue gas are difficult to recover, and the flue gas of heating furnace can be reduced. In order to improve the comprehensive thermal efficiency, increase the content of water vapor and reduce the content of NOx, etc.
- Summary
- Abstract
- Description
- Claims
- Application Information
AI Technical Summary
Problems solved by technology
Method used
Image
Examples
Embodiment 1
[0044] Please refer to figure 1 , this embodiment provides a heating furnace flue gas waste heat recovery system 100, which includes a spray cooling tower 110, which includes a cooling tower body 111, and a side of the cooling tower body 111 relatively close to the bottom of the tower is provided with a flue gas inlet 112 , and then the high-temperature flue gas formed in the heating furnace enters the spray cooling tower 110 through the flue gas inlet 112, and then realizes waste heat recovery of the flue gas.
[0045] It should be noted that the cooling tower body 111 is a conventional tower structure, the tower structure is set on the ground, the side relatively close to the ground is the bottom of the tower, and the side opposite to the bottom of the tower is the top of the tower.
[0046] The spray cooling tower 110 includes a first spray device 113 for spraying cooling liquid. The first spray device 113 is arranged in the cooling tower body 111 and is located on a side r...
Embodiment 2
[0068] see image 3 , this embodiment provides a heating furnace flue gas waste heat recovery system 200, which includes a spray cooling tower 210, the spray cooling tower 210 includes a cooling tower body 211, the cooling tower body 211 is provided with a cooling section 240 and a condensation section 250, the cooling Section 240 communicates with condensation section 250, cooling section 240 is relatively close to the bottom of the tower, and condensation section 250 is relatively close to the bottom of the tower. At the same time, the side of the cooling tower body 211 relatively close to the bottom of the tower is provided with a flue gas inlet 212, that is, the flue gas inlet 212 is located at In the cooling section 240.
[0069]The spray cooling tower 210 includes a first spray device 213 and a spray heat exchanger 214, the first spray device 213 and the spray heat exchanger 214 are all located in the cooling section 240, and the first spray device 213 is arranged on the...
Embodiment 3
[0093] This embodiment also provides a process of recovering waste heat from flue gas using the waste heat recovery system of heating furnace flue gas in Embodiment 2. The temperature and the temperature of different liquids are different, as follows:
[0094] The temperature of the flue gas flowing out of the heating furnace is 280°C, and the temperature of the flue gas is reduced to 100°C after passing through the air preheater; the temperature of the air entering the air preheater is 70°C; the air entering the heating spray heat exchanger is 50°C ℃; the flue gas temperature after the heat exchange of the first spraying device is 65 ℃; the temperature of the cooling water sprayed by the first spraying device is 64 ℃; the temperature of the condensate sprayed by the third spraying device is 52 ℃; the third spraying The flue gas temperature after heat exchange of the device is 53°C.
[0095] The air entering the air humidification tower is 0°C; the temperature of the water ac...
PUM
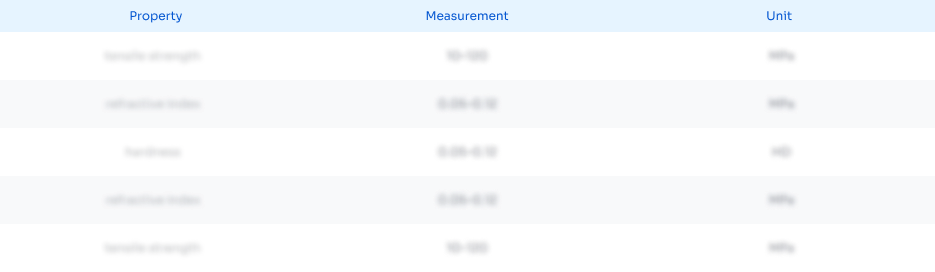
Abstract
Description
Claims
Application Information

- R&D
- Intellectual Property
- Life Sciences
- Materials
- Tech Scout
- Unparalleled Data Quality
- Higher Quality Content
- 60% Fewer Hallucinations
Browse by: Latest US Patents, China's latest patents, Technical Efficacy Thesaurus, Application Domain, Technology Topic, Popular Technical Reports.
© 2025 PatSnap. All rights reserved.Legal|Privacy policy|Modern Slavery Act Transparency Statement|Sitemap|About US| Contact US: help@patsnap.com