Integral forming method for porous composite structural part
A technology for composite materials and structural parts, applied in design optimization/simulation, instruments, calculations, etc., can solve the problems of increased risk of parts damage, immaturity, structural damage of composite materials, etc., to reduce the risk of damage and reduce Damage and defects, the effect of increasing strength
- Summary
- Abstract
- Description
- Claims
- Application Information
AI Technical Summary
Problems solved by technology
Method used
Image
Examples
Embodiment Construction
[0019] Disclosed is a method for the integral forming of thermoplastic composite structural parts containing holes, including a research method for the damage mechanism of the hole member and a complete process of laying path planning and optimization for guiding the integral forming of the hole member. The method can effectively reduce fiber breakage of thermoplastic composite hole parts, optimize internal force distribution, and improve mechanical properties of hole parts. This method will be described in detail below.
[0020] Step 1: Select the structural characteristics of typical hole parts, initially adopt a certain fiber direction, layup sequence, and single-layer thickness, establish a Cohesive 3D finite element model, apply loads / boundary constraints according to actual working conditions, and determine the structural stress through static analysis Distribution and the position where the maximum stress and strain appear; use the Hashin failure criterion to judge the ...
PUM
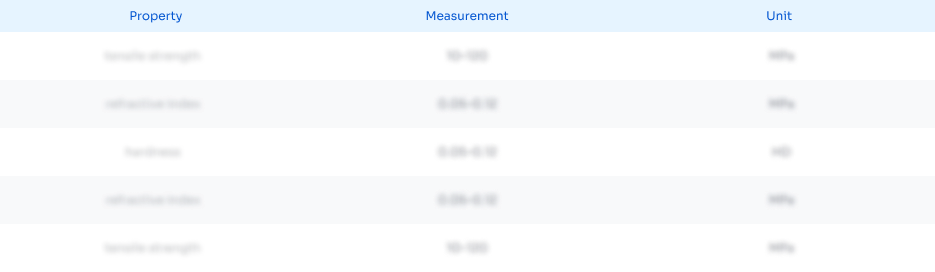
Abstract
Description
Claims
Application Information

- R&D Engineer
- R&D Manager
- IP Professional
- Industry Leading Data Capabilities
- Powerful AI technology
- Patent DNA Extraction
Browse by: Latest US Patents, China's latest patents, Technical Efficacy Thesaurus, Application Domain, Technology Topic, Popular Technical Reports.
© 2024 PatSnap. All rights reserved.Legal|Privacy policy|Modern Slavery Act Transparency Statement|Sitemap|About US| Contact US: help@patsnap.com