Method for recovering cobalt and lithium metals from waste lithium cobalt oxide battery
A technology of old lithium cobalt oxide and lithium metal, which is applied in the field of waste lithium ion battery treatment, can solve the problems of high consumption of acid and alkali and other chemical reagents, low selective extraction rate, and difficult disposal of waste liquid, achieving outstanding environmental benefits, Significant innovation, the effect of reducing reaction energy consumption
- Summary
- Abstract
- Description
- Claims
- Application Information
AI Technical Summary
Problems solved by technology
Method used
Image
Examples
Embodiment 1
[0041] A method for reclaiming cobalt and lithium metal from waste lithium cobalt oxide batteries, the specific steps are as follows:
[0042] (1) Immerse the waste lithium cobalt oxide battery (in the field of electronic communication) into a NaCl solution with a concentration of 10% for self-discharge treatment to prevent the explosion caused by the short circuit of the battery in subsequent operations, and the waste lithium cobalt oxide after the discharge is completed After the battery is manually disassembled or mechanically crushed, different parts including the positive electrode, negative electrode, diaphragm, and battery case are obtained. The positive electrode material is placed in a muffle furnace for calcination treatment. In an air atmosphere, the calcination temperature is 500°C and the calcination time is 2h. During the calcination process, the binder, conductive agent and electrolyte on the positive electrode material are pyrolyzed under high temperature condit...
Embodiment 2
[0046] A method for reclaiming cobalt and lithium metal from waste lithium cobalt oxide batteries, the specific steps are as follows:
[0047] (1) Immerse the waste lithium cobalt oxide battery (in the field of power vehicles) into a NaCl solution with a concentration of 20% for self-discharge treatment to prevent the explosion caused by the short circuit of the battery in subsequent operations, and the waste lithium cobalt oxide after the discharge is completed After the battery is manually disassembled or mechanically crushed, different parts including the positive electrode, negative electrode, separator, and battery case are obtained. The positive electrode material is placed in a muffle furnace for calcination treatment. In an air atmosphere, the calcination temperature is 600°C and the calcination time is 3h. During the calcination process, the binder, conductive agent and electrolyte on the positive electrode material are pyrolyzed under high temperature conditions, and ...
Embodiment 3
[0051] A method for reclaiming cobalt and lithium metal from waste lithium cobalt oxide batteries, the specific steps are as follows:
[0052] (1) Immerse the waste lithium cobalt oxide battery (infrastructure field) in a NaCl solution with a concentration of 30% for self-discharge treatment to prevent the explosion caused by the short circuit of the battery in subsequent operations. After the discharge is completed, the waste lithium cobalt oxide After the battery is manually disassembled or mechanically crushed, different parts including the positive electrode, negative electrode, separator, and battery case are obtained. The positive electrode material is placed in a muffle furnace for calcination treatment. The calcination temperature is 650 ° C and the calcination time is 4 hours in an air atmosphere. During the calcination process, the binder, conductive agent and electrolyte on the positive electrode material are pyrolyzed under high temperature conditions, and the lithi...
PUM
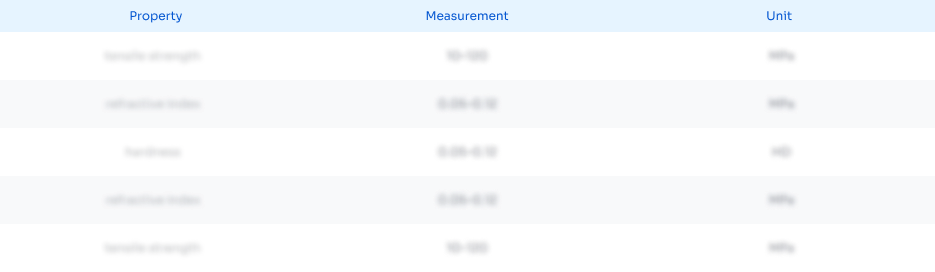
Abstract
Description
Claims
Application Information

- R&D
- Intellectual Property
- Life Sciences
- Materials
- Tech Scout
- Unparalleled Data Quality
- Higher Quality Content
- 60% Fewer Hallucinations
Browse by: Latest US Patents, China's latest patents, Technical Efficacy Thesaurus, Application Domain, Technology Topic, Popular Technical Reports.
© 2025 PatSnap. All rights reserved.Legal|Privacy policy|Modern Slavery Act Transparency Statement|Sitemap|About US| Contact US: help@patsnap.com