Method for recovering valuable elements in waste lithium ion battery electrode material
A technology for lithium ion batteries and electrode materials, which is applied in the field of recycling electrode materials for waste lithium batteries, can solve the problems of low nickel, cobalt and manganese leaching rate, increased cost, low recovery rate, etc., so as to reduce battery sorting and recovery costs, Achieving the effect of recycling and reducing recycling costs
- Summary
- Abstract
- Description
- Claims
- Application Information
AI Technical Summary
Problems solved by technology
Method used
Examples
Embodiment 1
[0012] After crushing and sorting waste lithium-ion batteries containing nickel-cobalt-manganese positive electrode materials, a mixture of positive electrode materials, negative electrode graphite powder and part of the electrolyte is obtained, containing 15%wt of nickel, 8%wt of cobalt, 10%wt of manganese, and 5% of lithium. %wt, carbon 35%wt, fluorine 1.2%wt, calcining under nitrogen atmosphere, the calcining temperature is 500 ℃, and keep it warm for 30 minutes. The roasted slag in [H + ] The sulfuric acid solution with a concentration of 0.5mol / L is mixed according to the mass ratio of 1:10, and leached at a leaching temperature of 90°C and a leaching time of 1h. After the leaching is completed, filter and separate to obtain the leaching solution and leaching residue; the leaching solution is used for further recovery of nickel and cobalt , manganese, lithium, and the leaching residue are used to prepare negative electrode materials. The analysis results show that the le...
Embodiment 2
[0014] After crushing and sorting waste lithium-ion batteries containing nickel-cobalt-aluminum cathode materials, a mixture of cathode materials, negative electrode graphite powder, and part of the electrolyte is obtained, containing 30%wt of nickel, 6%wt of cobalt, 5%wt of aluminum, and 4% of lithium. %wt, carbon 20%wt, fluorine 0.5%wt, calcined in an argon atmosphere, the calcined temperature is 600 ℃, and kept for 60 minutes. The roasted slag in [H + ] The hydrochloric acid solution with a concentration of 1mol / L is mixed according to the mass ratio of 1:8, and leached at a leaching temperature of 70°C and a leaching time of 3h. Manganese, lithium, and leached slag are used to prepare negative electrode materials. The analysis results show that the leaching rates in terms of slag are 90.97% for lithium, 92.75% for nickel, 91.78% for cobalt, and 90.77% for aluminum.
Embodiment 3
[0016] After crushing and sorting waste lithium-ion batteries containing different proportions of nickel-cobalt-manganese cathode materials, a mixture of cathode materials, negative electrode graphite powder, and part of the electrolyte is obtained, which contains 22%wt of nickel, 12%wt of cobalt, and 6% of manganese wt, aluminum 0.01%wt, lithium 2%wt, carbon 30%wt, fluorine 1.0%wt, were calcined in a carbon dioxide atmosphere at 400°C and kept for 120 minutes. The roasted slag in [H + ] Sulfuric acid solution and hydrochloric acid solution with a concentration of 2mol / L are mixed at a mass ratio of 1:6, and leached at a leaching temperature of 50°C and a leaching time of 5h. After the leaching is completed, filter and separate to obtain the leaching solution and leaching residue; the leaching solution is used to further recover nickel , cobalt, manganese, lithium, and the leaching residue are used to prepare negative electrode materials. The analysis results show that the le...
PUM
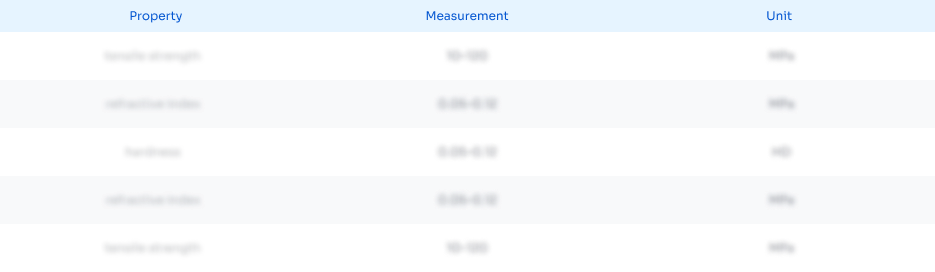
Abstract
Description
Claims
Application Information

- Generate Ideas
- Intellectual Property
- Life Sciences
- Materials
- Tech Scout
- Unparalleled Data Quality
- Higher Quality Content
- 60% Fewer Hallucinations
Browse by: Latest US Patents, China's latest patents, Technical Efficacy Thesaurus, Application Domain, Technology Topic, Popular Technical Reports.
© 2025 PatSnap. All rights reserved.Legal|Privacy policy|Modern Slavery Act Transparency Statement|Sitemap|About US| Contact US: help@patsnap.com