Corrosion process of anode foil for high-voltage aluminum electrolytic capacitor
A technology of aluminum electrolytic capacitors and anode foils, applied in electrolytic capacitors, capacitors, circuits, etc., can solve the problems of low capacity, low production line efficiency, poor hole consistency, etc., achieve high production efficiency, reduce environmental protection investment, and solve the problem of discoloration Effect
- Summary
- Abstract
- Description
- Claims
- Application Information
AI Technical Summary
Problems solved by technology
Method used
Image
Examples
Embodiment 1
[0043] The specific operation steps are as follows:
[0044] (1) Pretreatment: place the annealed electronic aluminum foil with a purity of 99.99% in a fluorine-containing acid solution with a concentration of 1 wt%, and treat it at 50°C for 2 minutes;
[0045] (2) Electrolysis for the first time porosity: The aluminum foil that has been pretreated and cleaned is subjected to the first stage of electrification treatment in a solution containing 30wt% sulfuric acid, 6wt% hydrochloric acid, and 0.4wt% aluminum ions at a temperature of 70°C and a current density of 0.25A / cm 2 , corroded for 25s;
[0046] (3) Electrolysis for the second porosity: the aluminum foil that has undergone the first porosity is subjected to a first-stage electrification treatment in a solution containing 30wt% sulfuric acid, 6wt% hydrochloric acid, and 0.6wt% aluminum ions at a temperature of 70°C and a current density of 0.25A / cm 2 , corroded for 25s;
[0047] (4) The third hole of electrolysis: the...
Embodiment 2
[0055] The specific operation steps are as follows:
[0056] (1) Pretreatment: place the annealed electronic aluminum foil with a purity of 99.99% in a fluorine-containing acid solution with a concentration of 1.0 wt%, and treat it at 45°C for 1.0 min;
[0057] (2) Electrolysis for the first time porosity: the pre-treated and cleaned aluminum foil is subjected to a first-stage electrification treatment in a solution containing 30wt% sulfuric acid, 3wt% hydrochloric acid, and 0.4wt% aluminum ions at a temperature of 69°C and a current density of 0.20 / cm 2 , corroded for 30s;
[0058] (3) Electrolysis for the second hole: the aluminum foil that has passed through the first hole is subjected to the first stage of electrification treatment in a solution containing 30wt% sulfuric acid, 3wt% hydrochloric acid, and 0.6wt% aluminum ions. The temperature is 69 ° C, and the current density 0.20A / cm 2 , corroded for 30s;
[0059] (4) The third hole of electrolysis: the aluminum foil ...
PUM
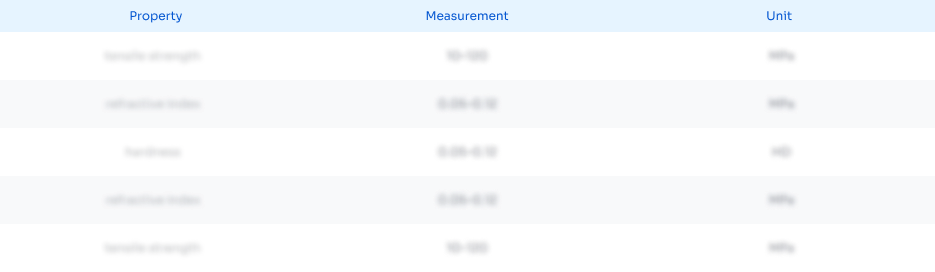
Abstract
Description
Claims
Application Information

- R&D
- Intellectual Property
- Life Sciences
- Materials
- Tech Scout
- Unparalleled Data Quality
- Higher Quality Content
- 60% Fewer Hallucinations
Browse by: Latest US Patents, China's latest patents, Technical Efficacy Thesaurus, Application Domain, Technology Topic, Popular Technical Reports.
© 2025 PatSnap. All rights reserved.Legal|Privacy policy|Modern Slavery Act Transparency Statement|Sitemap|About US| Contact US: help@patsnap.com