Colored glaze material, process for firing colored glaze material into molten base material, and application of colored glaze material
A melting and glazed technology, applied in the production of ceramic materials, furnaces, furnace types, etc., can solve the problems of color floating and glaze being too transparent, and achieve the effect of color floating, beautiful and thick finished products, and good product stability.
- Summary
- Abstract
- Description
- Claims
- Application Information
AI Technical Summary
Problems solved by technology
Method used
Image
Examples
Embodiment 1
[0024] 1) Prepare materials according to the following raw materials by weight: 100 parts of quartz sand, 40 parts of sodium hydroxide, 10 parts of potassium carbonate, 8 parts of borax, 15 parts of feldspar powder, 3 parts of calcium carbonate powder, 8 parts of aluminum oxide, 12 parts of zinc oxide, 14 parts of sodium fluorosilicate, 0.5 parts of antimony oxide, 2 parts of sodium chloride, 2 parts of cadmium yellow, and 0.55 parts of selenium powder; mix the raw materials and stabilize the temperature of the kiln at 1400 °C;
[0025] 2) Put in the raw material with a mixing volume of 53%, melt it to a semi-molten state after 240 minutes, and stir it evenly with an iron stirring rod;
[0026] 3) Then add 22% raw materials for the second time, continue to melt for 120 minutes, and use an iron stirring rod to stir evenly;
[0027] 4) Put all the remaining raw materials into the crucible and seal it, continue to melt for 360 minutes, then unseal, cool down to 1300°C and keep it...
Embodiment 2
[0030] 1) Prepare materials according to the following raw materials by weight: 100 parts of quartz sand, 38.6 parts of sodium hydroxide, 11.1 parts of potassium carbonate, 7.2 parts of borax, 15.8 parts of feldspar powder, 2.6 parts of calcium carbonate powder, 8.7 parts of aluminum oxide, 11.3 parts of zinc oxide, 15.4 parts of sodium fluorosilicate, 0.42 parts of antimony oxide, 2.3 parts of sodium chloride, 1.8 parts of cadmium yellow, and 0.61 parts of selenium powder; mix the raw materials and stabilize the temperature of the kiln at 1401 °C;
[0031] 2) Put in 50% of the raw material, melt it to a semi-molten state after 260 minutes, and stir it evenly with an iron stirring rod;
[0032] 3) Then add 25% raw materials for the second time, continue to melt for 115 minutes, and use an iron stirring rod to stir evenly;
[0033] 4) Put all the remaining raw materials into the crucible and seal it, continue to melt for 370 minutes, then unseal, cool down to 1302°C and keep it...
Embodiment 3
[0036] 1) Prepare materials according to the following raw materials by weight: 100 parts of quartz sand, 41.3 parts of sodium hydroxide, 8.7 parts of potassium carbonate, 8.6 parts of borax, 14 parts of feldspar powder, 3.4 parts of calcium carbonate powder, 7.5 parts of aluminum oxide, 12.3 parts of zinc oxide , 12.4 parts of sodium fluorosilicate, 0.61 parts of antimony oxide, 1.7 parts of sodium chloride, 2.1 parts of cadmium yellow, 0.5 parts of selenium powder, and 4 parts of yellow pigment; mix the raw materials and stabilize the temperature of the kiln at 1399 ° C;
[0037] 2) Put in raw materials with a mixing volume of 55%, melt them to a semi-molten state after 220 minutes, and stir them evenly with an iron stirring rod;
[0038] 3) Then put in 20% raw materials for the second time, continue to melt for 130 minutes, and stir evenly with an iron stirring rod;
[0039] 4) Put all the remaining raw materials into the crucible and seal it, continue to melt for 360 minut...
PUM
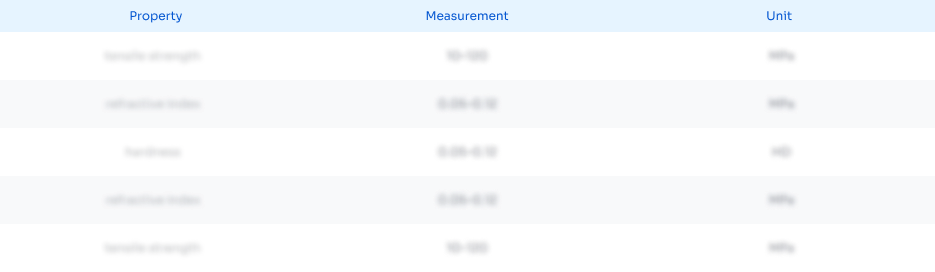
Abstract
Description
Claims
Application Information

- R&D
- Intellectual Property
- Life Sciences
- Materials
- Tech Scout
- Unparalleled Data Quality
- Higher Quality Content
- 60% Fewer Hallucinations
Browse by: Latest US Patents, China's latest patents, Technical Efficacy Thesaurus, Application Domain, Technology Topic, Popular Technical Reports.
© 2025 PatSnap. All rights reserved.Legal|Privacy policy|Modern Slavery Act Transparency Statement|Sitemap|About US| Contact US: help@patsnap.com