Elastic-Hysteretic Low Frequency Large Displacement Vibration Isolator Based on Electromagnetic Negative Stiffness
A negative stiffness and vibration isolator technology, applied in the functional characteristics of springs/shock absorbers, springs/shock absorbers, springs, etc., can solve the problem of increasing the internal damping and energy dissipation performance of the vibration isolation system, and there is no vibration damping device that has a large low frequency. Displacement vibration response, difficult to achieve efficient isolation and other problems, to achieve the effect of simple structure, strong bearing capacity and small size
- Summary
- Abstract
- Description
- Claims
- Application Information
AI Technical Summary
Problems solved by technology
Method used
Image
Examples
Embodiment Construction
[0039] see figure 1 , the structural form of the elastic-hysteretic low-frequency large-displacement vibration isolator based on electromagnetic negative stiffness in this embodiment is:
[0040] The upper platform 1 and the lower platform 21 are connected by 6 arched beam springs 7 with the same structure distributed on the outer periphery at equal intervals, and the arched beam springs 7 constrain the upper platform 1 to move relative to the lower platform 21 only in the axial direction.
[0041]On the lower platform 21, the electromagnetic negative stiffness spring composed of the inner magnetic ring 14, the outer magnetic ring 15 and the electromagnetic coil 18 is fixedly arranged, and the electromagnetic negative stiffness spring is connected in parallel with the second leaf spring 8 and the third leaf spring 19 to form a real-time adjustable electromagnetic spring. The bistable mechanism, the electromagnetic bistable mechanism is configured in series with the first leaf ...
PUM
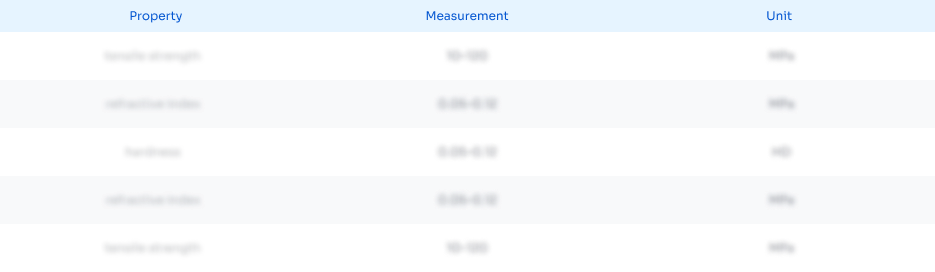
Abstract
Description
Claims
Application Information

- R&D
- Intellectual Property
- Life Sciences
- Materials
- Tech Scout
- Unparalleled Data Quality
- Higher Quality Content
- 60% Fewer Hallucinations
Browse by: Latest US Patents, China's latest patents, Technical Efficacy Thesaurus, Application Domain, Technology Topic, Popular Technical Reports.
© 2025 PatSnap. All rights reserved.Legal|Privacy policy|Modern Slavery Act Transparency Statement|Sitemap|About US| Contact US: help@patsnap.com