Near-net forging forming method for aluminum alloy special-shaped shell precision forge piece
A precision forging and aluminum alloy technology, applied in the field of forging processing, can solve the problems of large cylinder wall thickness, unsuitable special-shaped thin-walled shell, etc.
- Summary
- Abstract
- Description
- Claims
- Application Information
AI Technical Summary
Problems solved by technology
Method used
Image
Examples
Embodiment 1
[0047] Such as figure 1Shown, a kind of warm extrusion mold comprises lower mold assembly and the upper mold assembly that is arranged on this lower mold assembly, and described lower mold assembly comprises extrusion mold lower template A9, and this extrusion mold lower template A9 is provided with an extrusion die lower die base A11, and the extrusion die lower die base A11 is sequentially embedded with an extrusion die lower die backing plate A8, an extrusion die lower die backing block A13 and a combined die . The lower die base A11 of the extrusion die is connected with the lower template A9 of the extrusion die by bolts. The combined die includes a die outer casing A7, a die core A14 and a die core pad A15 that are sheathed together from outside to inside in sequence. The extrusion die lower die pressing plate A6 is step-fitted with the die outer cover A7, and covers the upper end of the extrusion die lower die base A11, and the extrusion die lower die pressing plate A...
Embodiment 2
[0054] Such as figure 2 As shown, a warm stamping die includes a stamping die lower template 12 and a lower die 7 installed on the stamping die lower template 12, and a stamping die cavity 7a is opened on the upper surface of the lower die 7. The upper die base 2 of the punching die is provided above the lower die 7, and the die handle 1 is connected above the upper die base 2 of the stamping die. The surface is provided with an upper die 4, on which a stamping die punch 6 is installed, and the lower end of the stamping die punch 6 faces the stamping die cavity 7a.
[0055] The stamping die concave mold cavity 7a includes an upper disc portion and a lower special-shaped constriction portion, and the disc portion communicates with the special-shaped constriction portion to form the stamping die concave mold cavity 7a. The lower mold 7 and the lower template 12 of the stamping die below the concave mold cavity 7a of the stamping die have a stamping die ejecting hole, which is ...
Embodiment 3
[0063] A near-net forging forming method for precision forgings of aluminum alloy special-shaped shells is carried out according to the following steps:
[0064] Step 1, blanking: saw the 2A12 hard aluminum alloy round bar with a size of Φ28mm and cut it into a cylindrical blank. The blank is as follows image 3 shown;
[0065] Step 2. Warm extrusion billet making: install the warm extrusion die of Example 1 on a YA32-100 four-column hydraulic press, and preheat the die with a blowtorch or a heated billet, and the preheating temperature is about 200°C , apply lard evenly with a brush to the surface of the extrusion die punch of the warm extrusion die and the concave cavity of the extrusion die, heat the billet to 420°C, keep it warm for 25min, and use XCT101 temperature controller to control Warm, dip in lard then, put into the extrusion die cavity of the warm extrusion mold of embodiment 1 fast again;
[0066] Warm extrusion is performed on the billet to obtain an extruded ...
PUM
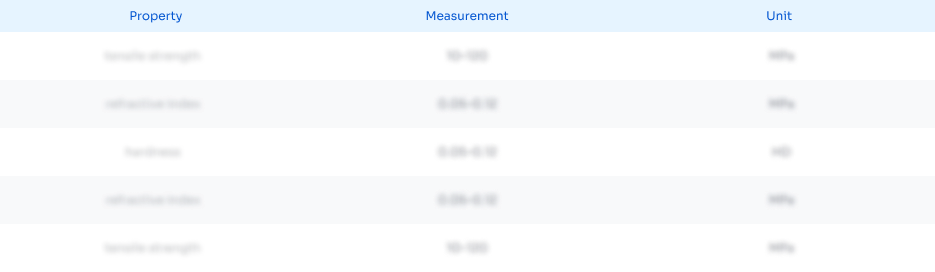
Abstract
Description
Claims
Application Information

- R&D
- Intellectual Property
- Life Sciences
- Materials
- Tech Scout
- Unparalleled Data Quality
- Higher Quality Content
- 60% Fewer Hallucinations
Browse by: Latest US Patents, China's latest patents, Technical Efficacy Thesaurus, Application Domain, Technology Topic, Popular Technical Reports.
© 2025 PatSnap. All rights reserved.Legal|Privacy policy|Modern Slavery Act Transparency Statement|Sitemap|About US| Contact US: help@patsnap.com