Method for preparing porous silicon/carbon/nano metal composite negative electrode material by plasma activated cutting of silicon waste
A technology of plasma activation and carbon composite material, which is applied in the field of new energy materials and electrochemistry, can solve the problems of difficult recovery of diamond wire-cut silicon waste, shortening the transmission distance of lithium ions and electrons, and low volumetric conductivity, saving raw materials. cost, reducing absolute volume effects, overcoming the effects of low conductivity
- Summary
- Abstract
- Description
- Claims
- Application Information
AI Technical Summary
Problems solved by technology
Method used
Image
Examples
Embodiment 1
[0028] Example 1: A method for preparing porous silicon / carbon / nano-metal composite anode material by cutting silicon waste through plasma activation, the specific steps are as follows:
[0029] (1) The diamond wire cutting silicon waste of photovoltaics is crushed, ground, and vacuum dried for 4 hours to obtain waste silicon powder;
[0030] (2) Mix the waste silicon powder and carbon source in step (1) in a high-energy ball mill, pass through a 300-mesh sieve, and vacuum-dry for 24 hours to obtain a silicon-carbon mixed powder, wherein the mass fraction of the waste silicon powder in the silicon-carbon mixed powder is 50 %;
[0031] (3) Pass pure argon gas into the plasma furnace to remove the air in the furnace body, and use argon gas as the protective gas and carrier gas, and pass the silicon-carbon mixed powder in step (2) into the plasma furnace through the powder feeding device. Plasma activation treatment, gasification, condensation and recrystallization of silicon-ca...
Embodiment 2
[0036] Embodiment 2: A method for preparing porous silicon / carbon / nano-metal composite negative electrode material by cutting silicon waste through plasma activation, the specific steps are as follows:
[0037] (1) The diamond wire cutting silicon waste of photovoltaics is crushed, ground, and vacuum dried for 4 hours to obtain waste silicon powder;
[0038] (2) Mix the waste silicon powder and carbon source in step (1) in a high-energy ball mill, pass through a 300-mesh sieve, and vacuum-dry for 18 hours to obtain a silicon-carbon mixed powder, wherein the mass fraction of the waste silicon powder in the silicon-carbon mixed powder is 60 %;
[0039] (3) Pass pure argon gas into the plasma furnace to remove the air in the furnace body, and use argon gas as the protective gas and carrier gas, and pass the silicon-carbon mixed powder in step (2) into the plasma furnace through the powder feeding device. Plasma activation treatment, gasification, condensation and recrystallizati...
Embodiment 3
[0041] Embodiment 3: A method for preparing porous silicon / carbon / nano-metal composite anode material by cutting silicon waste through plasma activation, the specific steps are as follows:
[0042] (1) The diamond wire cutting silicon waste of photovoltaics is crushed, ground, and vacuum dried for 3 hours to obtain waste silicon powder;
[0043] (2) Mix the waste silicon powder and carbon source in step (1) in a high-energy ball mill, pass through a 300-mesh sieve, and vacuum-dry for 24 hours to obtain a silicon-carbon mixed powder, wherein the mass fraction of the waste silicon powder in the silicon-carbon mixed powder is 60 %;
[0044] (3) Pass pure argon gas into the plasma furnace to remove the air in the furnace body, and use argon gas as the protective gas and carrier gas, and pass the silicon-carbon mixed powder in step (2) into the plasma furnace through the powder feeding device. Plasma activation treatment, gasification, condensation and recrystallization of silicon...
PUM
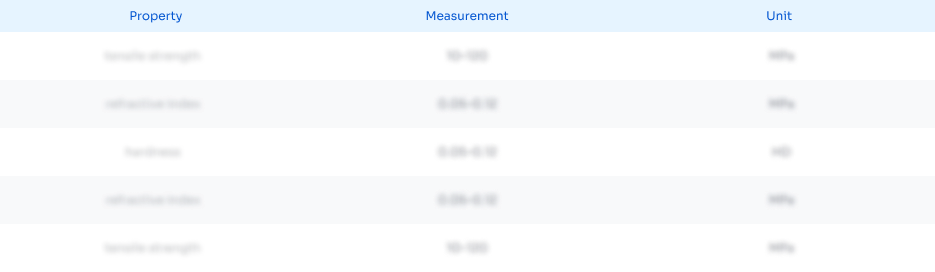
Abstract
Description
Claims
Application Information

- Generate Ideas
- Intellectual Property
- Life Sciences
- Materials
- Tech Scout
- Unparalleled Data Quality
- Higher Quality Content
- 60% Fewer Hallucinations
Browse by: Latest US Patents, China's latest patents, Technical Efficacy Thesaurus, Application Domain, Technology Topic, Popular Technical Reports.
© 2025 PatSnap. All rights reserved.Legal|Privacy policy|Modern Slavery Act Transparency Statement|Sitemap|About US| Contact US: help@patsnap.com