Method for improving density and component uniformity of selected area laser melting product
A selective laser melting and densification technology, which is applied in the directions of improving energy efficiency, process efficiency, and additive processing, etc., can solve the problems of uneven distribution of components, obstacles to the development of laser in-situ synthesis technology, and low densities. Promotes uniform spreading, generation suppression, and defect suppression effects
- Summary
- Abstract
- Description
- Claims
- Application Information
AI Technical Summary
Problems solved by technology
Method used
Image
Examples
Embodiment 1
[0028] A method for improving the density and composition uniformity of selected laser melting products, including the following steps:
[0029] Step 1, raw materials are mixed, the mixed powder is in accordance with FeCoCrNiSi 0.05 The atomic ratio is configured to mix in a three-dimensional mixer for 3 hours, the cylinder speed is 30r / min, and the uniformly mixed powder is dried in a vacuum dryer for 8 hours at a temperature of 80 degrees Celsius, and the vacuum is less than 10KPa absolute pressure. After completion, sealed and preserved to obtain high-entropy alloy powder.
[0030] Step 2. Additive preparation. The substrate is made of 316L stainless steel with a size of 250×250×15mm. The surface of the substrate is polished with an angle grinder until there is no oxide. The oil and dirt on the surface are cleaned with acetone and alcohol respectively. Put the high-entropy alloy powder obtained after the completion of the step 1 into the printer silo, and use the AM-400 laser 3D...
Embodiment 2
[0040] A method to improve the density and composition uniformity of laser melting products in selected areas:
[0041] Printing of FeCoCrNiMn alloy powder based on SLM technology. Since the alloy powder has undergone repeated component blending in the powdering process, there is no obvious segregation in the component distribution, and the method of the invention can improve its density.
[0042] For additive preparation, the substrate is made of 316L stainless steel with a size of 250×250×15mm. The surface of the substrate is polished with an angle grinder until there is no oxide. The oil and dirt on the surface are cleaned with acetone and alcohol respectively, and the FeCoCrNiMn alloy The powder is put into the printer silo, the AM-400 laser 3D printing equipment produced by Renishaw is used for laser additive manufacturing, and a block with a size of 6mm×6mm×6mm is constructed in Renishaw-QuantAM, and the rotation angle between layers is set It is 67° to release the residual ...
Embodiment 3
[0047] A method for improving the density and composition uniformity of selected laser melting products, including the following steps:
[0048] Printing of FeCoCrNi alloy powder based on SLM technology. Since the alloy powder has undergone repeated component blending in the powdering process, there is no obvious segregation in the component distribution, and the method of the invention can improve its density.
[0049] For additive preparation, the substrate is made of 316L stainless steel with a size of 250×250×15mm. The surface of the substrate is polished with an angle grinder until there is no oxide. The oil and dirt on the surface are cleaned with acetone and alcohol respectively, and the FeCoCrNi alloy The powder is put into the printer silo, and the AM-400 laser 3D printing equipment produced by Renishaw is used for laser additive manufacturing, and a block with a size of 6mm×6mm×6mm is constructed in Renishaw-QuantAM, and the rotation angle between layers is set It is 67°...
PUM
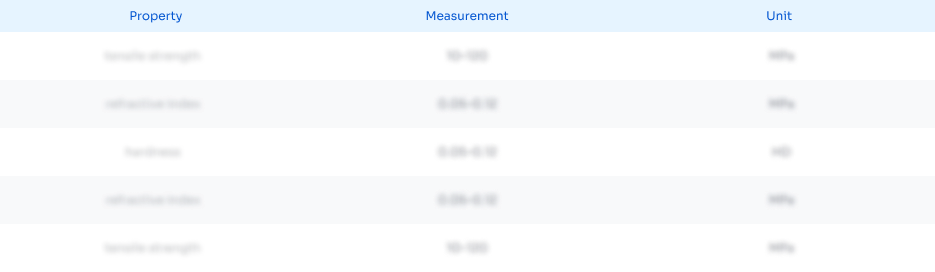
Abstract
Description
Claims
Application Information

- R&D
- Intellectual Property
- Life Sciences
- Materials
- Tech Scout
- Unparalleled Data Quality
- Higher Quality Content
- 60% Fewer Hallucinations
Browse by: Latest US Patents, China's latest patents, Technical Efficacy Thesaurus, Application Domain, Technology Topic, Popular Technical Reports.
© 2025 PatSnap. All rights reserved.Legal|Privacy policy|Modern Slavery Act Transparency Statement|Sitemap|About US| Contact US: help@patsnap.com