Hydrophilic melt-blown fabric and preparation method thereof
A technology of melt-blown cloth and hydrophilic type, which is applied in the direction of melt spinning, non-woven fabric, filament/thread forming, etc., can solve the problems of lack of micropores and gaps, poor hydrophilicity, etc., and achieve a simple and good preparation method Effects of hydrophilic properties and good antibacterial properties
- Summary
- Abstract
- Description
- Claims
- Application Information
AI Technical Summary
Problems solved by technology
Method used
Image
Examples
Embodiment 1
[0031] The preparation method of embodiment 1 hydrophilic type meltblown cloth
[0032] S1. The preparation method of hydrophilic modified polypropylene is as follows: 70g of 3-butene-1-amine monomer, 100g of polypropylene and 0.1g of tert-butyl peroxybenzoate are mixed, heated to 200°C to melt, and graft copolymerization occurs React for 1 hour, then add 100 mL of 0.5 mol / dilute hydrochloric acid to soak and react for 0.5 hours, filter, dry at 100°C to constant weight, then feed into a screw extruder, heat to 180°C, extrude, cool, and finally cut into uniform Hydrophilic modified polypropylene, the chemical structural formula is shown in formula Ⅰ:
[0033]
[0034] Formula I;
[0035] S2. Preparation of hydrophilic modified polypropylene fiber: Add 100g of hydrophilic modified polypropylene into the screw injection molding machine, heat and melt the filaments, the heating and melting temperature is 180°C, and stretch under the action of hot air to obtain hydrophilic Mod...
Embodiment 2
[0041] The preparation method of embodiment 2 hydrophilic type meltblown cloth
[0042] S1. The preparation method of hydrophilic modified polypropylene is as follows: 100g of 3-butene-1-amine monomer, 150g of polypropylene and 1g of potassium persulfate are mixed, heated to 230°C to melt, and graft copolymerization takes place for 3 hours, then, Add 200mL2mol / dilute hydrochloric acid to soak for 2 hours, filter, dry at 105°C to constant weight, then feed into a screw extruder, heat to 200°C, extrude, cool, and finally cut into uniform hydrophilic modified polypropylene;
[0043] S2. Preparation of hydrophilic modified polypropylene fiber: Add 100g of hydrophilic modified polypropylene into the screw injection molding machine, heat and melt the filaments, the heating and melting temperature is 220°C, and stretch under the action of hot air to obtain hydrophilic Modified polypropylene fiber;
[0044] S3. Preparation of melt-blown yarn: the hydrophilic modified polypropylene fi...
Embodiment 3
[0049] The preparation method of embodiment 3 hydrophilic type meltblown cloth
[0050] S1. The preparation method of hydrophilic modified polypropylene is as follows: 85g of 3-butene-1-amine monomer, 125g of polypropylene and 0.5g of azobisisobutyronitrile are mixed, heated to 215°C to melt, and graft copolymerization occurs 2h, then add 200mL of 1.2mol / dilute hydrochloric acid to soak for 1h, filter, dry at 102°C to constant weight, then feed into a screw extruder, heat to 190°C, extrude, cool, and finally cut into uniform hydrophilic Modified polypropylene;
[0051] S2. Preparation of hydrophilic modified polypropylene fiber: Add 100g of hydrophilic modified polypropylene into the screw injection molding machine, heat and melt the filaments, the heating and melting temperature is 200°C, and stretch under the action of hot air to obtain hydrophilic Modified polypropylene fiber;
[0052] S3. Preparation of melt-blown yarn: the hydrophilic modified polypropylene fiber is dra...
PUM
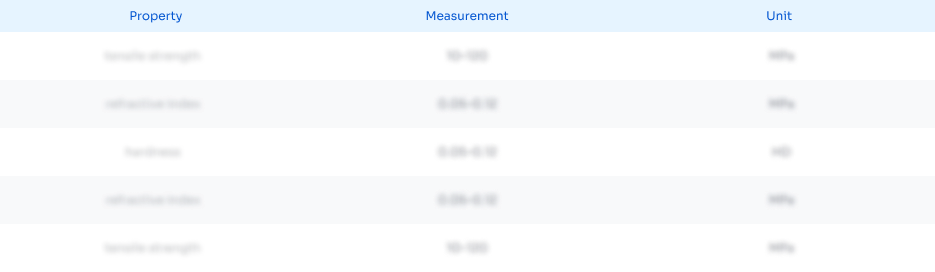
Abstract
Description
Claims
Application Information

- R&D Engineer
- R&D Manager
- IP Professional
- Industry Leading Data Capabilities
- Powerful AI technology
- Patent DNA Extraction
Browse by: Latest US Patents, China's latest patents, Technical Efficacy Thesaurus, Application Domain, Technology Topic, Popular Technical Reports.
© 2024 PatSnap. All rights reserved.Legal|Privacy policy|Modern Slavery Act Transparency Statement|Sitemap|About US| Contact US: help@patsnap.com